The Urban Infra Revolution project Journal 5: get an update about Lappeenranta's project
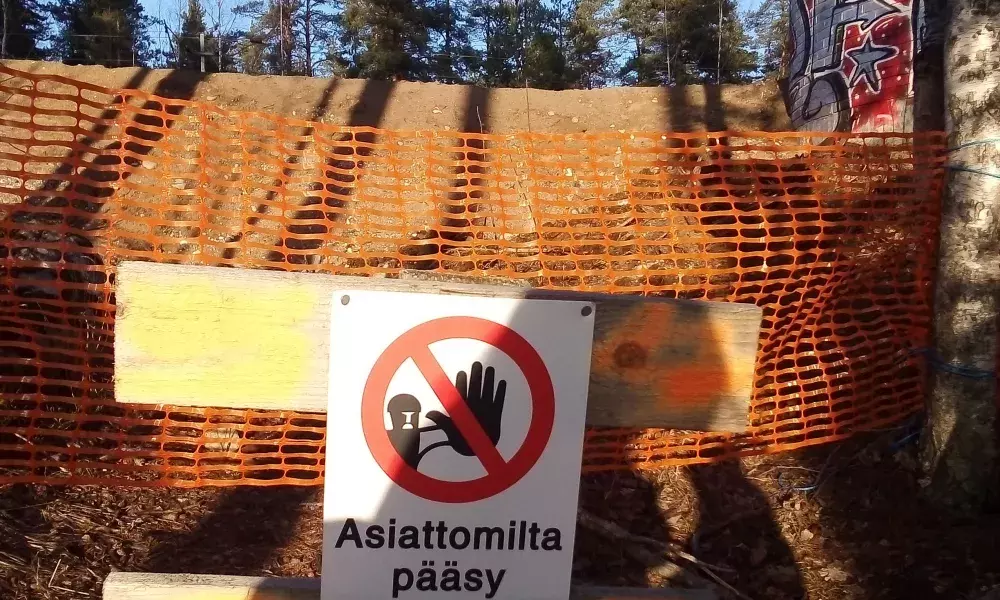
Executive summary
Despite the crisis caused by the COVID-19 pandemic, the work of the project has continued, and a significant progress has been made. This progress was presented during the online conference on 27 October 2020, as described in the second section of the article.
The third section provides detailed analysis of the project status, especially in the area of the development of the prototype as an innovative technical solution. Currently, the full-scale 3D printer is operational and uses new types of materials. The very intensive work for completing the construction of the prototype – the noise wall – is being carried out. The specific elements required for the new construction are manufactured daily, and the innovative project is close to becoming a reality. Moreover, the activities related to the certification of the new materials are being continued, and the environmental research is almost completed.
The fourth section of the article gives information on the different areas of project implementation. The project has been extended till December 2020, because of the restrictions imposed due to the COVID-19 pandemic that influenced the timely completion of the project. Considering the determination of the consortium members, the new deadline seems realistic. This chapter shows challenges addressed by the project during the last 6 months. There are presented in the following areas: leadership for implementation, public procurement, integrated cross-departmental working, adopting a participative approach, monitoring and evaluation, communicating with target beneficiaries, upscaling and others.
The last section presents the plans for the next three months. Despite the difficulties, the consortium in planning to finalise the project according to the new schedule – till the end of 2020. The commitment of the consortium members will make the project plan a reality.
Despite the crisis caused by the COVID-19 pandemic, the work of the project has continued, and a significant progress has been made. This progress was presented during the online conference on 27 October 2020, as described in the second section of the article.
The third section provides detailed analysis of the project status, especially in the area of the development of the prototype as an innovative technical solution. Currently, the full-scale 3D printer is operational and uses new types of materials. The very intensive work for completing the construction of the prototype – the noise wall – is being carried out. The specific elements required for the new construction are manufactured daily, and the innovative project is close to becoming a reality. Moreover, the activities related to the certification of the new materials are being continued, and the environmental research is almost completed.
The fourth section of the article gives information on the different areas of project implementation. The project has been extended till December 2020, because of the restrictions imposed due to the COVID-19 pandemic that influenced the timely completion of the project. Considering the determination of the consortium members, the new deadline seems realistic. This chapter shows challenges addressed by the project during the last 6 months. There are presented in the following areas: leadership for implementation, public procurement, integrated cross-departmental working, adopting a participative approach, monitoring and evaluation, communicating with target beneficiaries, upscaling and others.
The last section presents the plans for the next three months. Despite the difficulties, the consortium in planning to finalise the project according to the new schedule – till the end of 2020. The commitment of the consortium members will make the project plan a reality.
Introduction
Currently, the UIR project is in the last phase of implementation. The consortium has received all the necessary formal documents for the planned prototype realisation – the noise wall, and the process of scaling-up has started. Despite the ongoing pandemic, the construction work is being continued. Consecutive milestones have been achieved, and the progress is noticeable.
The main role in the last period was played by the Fimatec company. It has built a full-scale 3D printer in the warehouse, where the first industrial trials were conducted. The main concept of the 3D printer is based on devices dedicated for concrete materials. The first test showed that many changes are needed, including a pumping system. The new material prepared in the project requires significantly different solutions comparison with a traditional concrete. The innovative solutions were implemented into the manufacturing system and the production of ready-made components for the noise wall started. Presently, these components are being installed on the place where ground works were carried out, i.e. behind the kinder garden and the school, where it will block the noise from railway trains.
At the same time, other works in the project are being continued. The issues related to circular economy, sustainability, and life cycle assessment in the development of products based on secondary raw materials are widely discussed according to the Lappeenranta University. The theoretical background for the business models and ecosystems of products based on secondary raw materials has been created, and the first steps for its implementation in South Karelia have been undertaken. The important element of the project are the plans connected with product certification and normalisation that allows for using the project effect after the project duration. The certification procedures will required advanced research on the products, especially confirmation the safety the using secondary raw materials for the manufacturing the construction elements.
The progress of the project was presented in the online conference “Construction revolution begins in South Karelia - Urban Infra Revolution” on 27 October 2020. The conference stressed the possibility of using products from the local circular economy to replace binders (i.e. concrete) and support structures (i.e. concrete reinforcement) with prefabricated building elements. The raw materials for the building elements were separated from the side streams and construction waste of the local industry. Next, they were used to make a binder for the manufacturing of geopolymers (concrete-like materials). These materials find application in 3D printing technology. The main results of the developed technology are sustainable (low-carbon) and cost-efficient materials that provide new aesthetic possibilities and a manufacturing process that enables innovative construction.
1. Project update
The recipes of five materials for preparing geopolymers dedicated to 3D printing technology were designed by Apila Group (Figure 1.). The final product was named GEOPOCIT®. It is based on secondary raw materials such as residues, side streams, side products and other wastes.
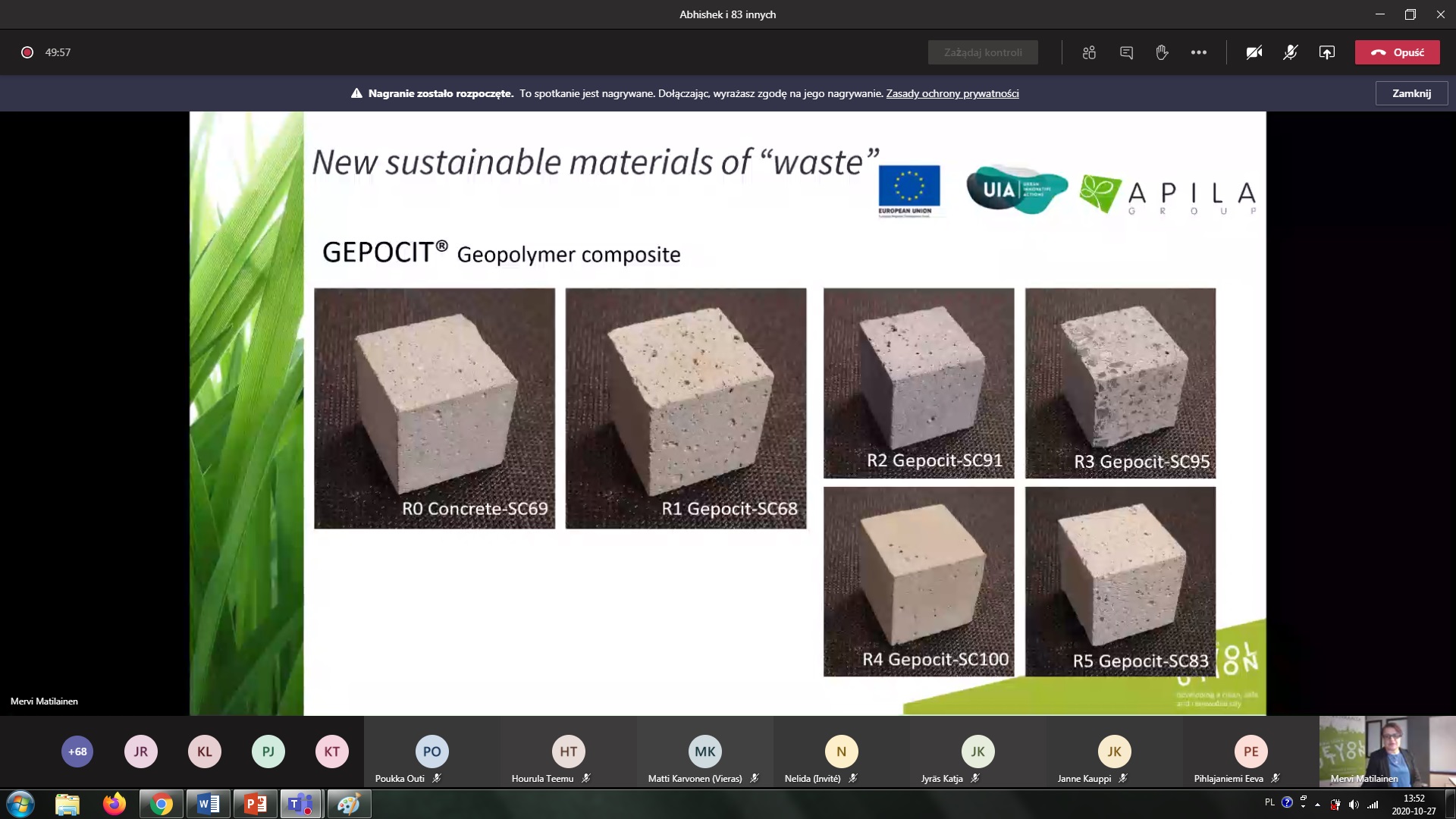
The following raw materials were considered during designing of new materials: flotation sand, green liquor sludge, ashes and waste fibres (side streams of the forest industry). For the final composition, the following materials were mainly used: ashes, slags, mineral tailings and waste rocks. The main criteria for the selection this particular composition were: material properties, material arability and price and possibilities to use waste as a raw materials (the design of the eco-friendly solutions). The project emphasises on new products by using the functionalised approach that will have a strong societal and environmental impact, such as energy efficiency, reduction of carbon footprint, waste reduction and development of idea of circular economy. To achieve this goal, the compositions included 68–100% waste materials.
The next step was to ensure that the materials are safe for environment and have sufficient mechanical properties for applications in the construction industry. Leaching tests confirmed that the elements are permanently bonded in the material and safe for the environment. The results of the leaching tests are in accordance with the EU standards; therefore, they confirmed environmental safety, including lack of hazardous and toxic elements. The tests of mechanical properties also yielded reasonable results. The compressive strength was 15–45 MPa, and the flexural strength was 3.5–9 MPa. These values are comparable to those of concrete materials for building applications.
The main challenge in the last period was to ensure that the materials are suitable for additive manufacturing technology on a large scale. Previously, the materials were tested on a small printer in Apila’s laboratory by using a robotic arm. At the current stage, the materials were used for a large-scale 3D printer. The test revealed some issues related to pumpability of the materials. These issues were resolved by making some changes in the construction of the 3D printer. This stage did not require any changes in material recipes.
Future challenges in this area are associated with investigation of durability in long term. Although these tests are not included in the project framework, they are planned and will be conducted after the project. These tests will enable to gain new knowledge on geopolymer composite based on waste or by-products.
Furthermore, legislative activities related to the project are being continued. The new material must be certified before it is launched in the market. Although it is not necessary to have all the required certificates for prototype application, certification is crucial for future implementation on a large scale. The consortium plans long-term tests on the prototypes performed during the project to confirm the safety of the created material.
Currently, the main challenge is the process of scaling up, taking into consideration the sustainability of the technology. The material for prototype manufacturing has been prepared, and the consortium is building a large-scale 3D printer device. The large-scale prototype is based on the experience gained from 3D printing of traditional concrete by Fimatec company. The large-scale 3D printer was constructed from a bed made for a printer cast on the warehouse floor. This work was necessary because the platform should be as flat as possible and easy to undertake maintenance work such as washing. It is particularly important for geopolymers, because they are more contagious and difficult to remove after hardening than traditional concrete (Figure 2).
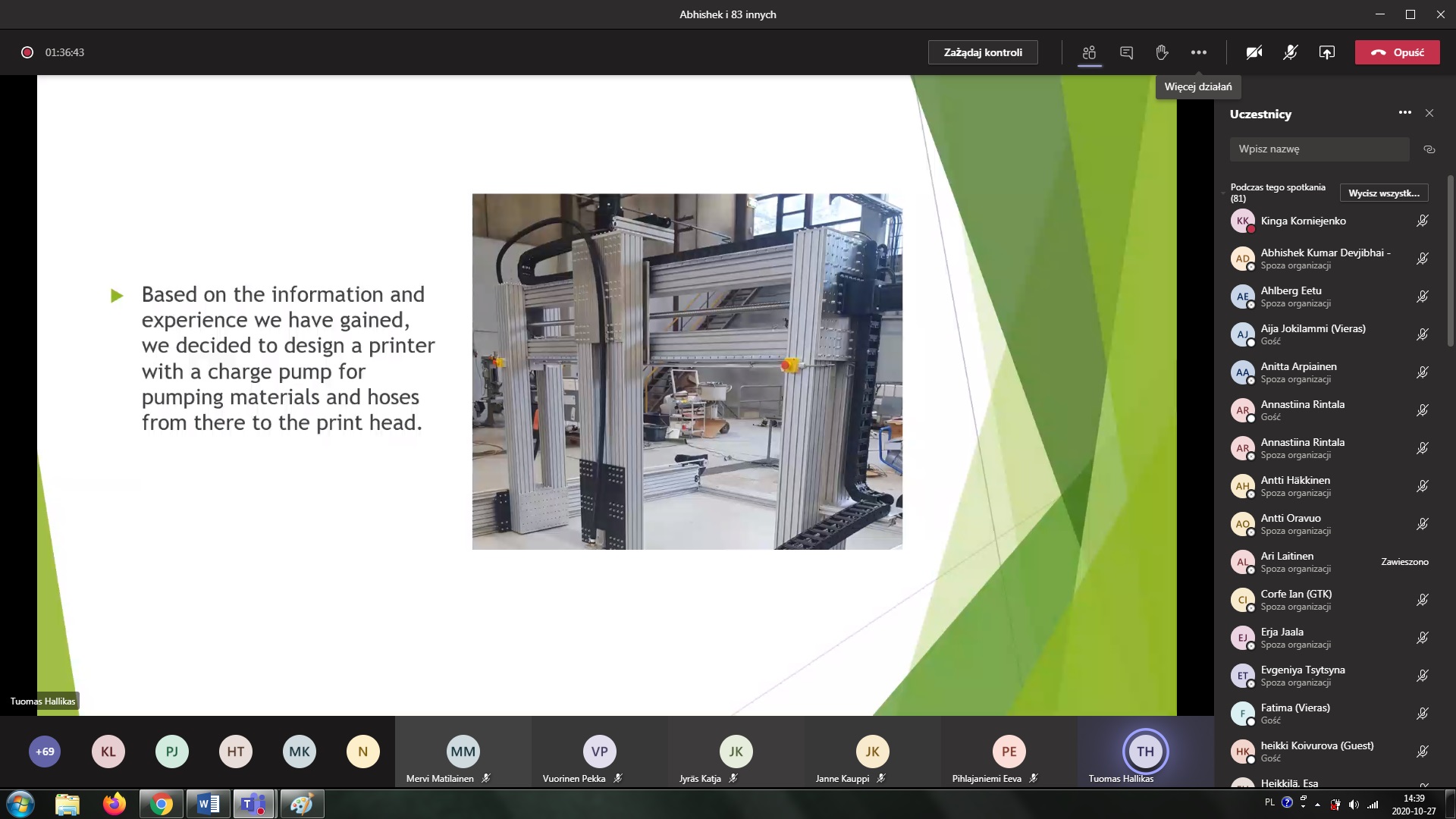
After the successful laboratory trials conducted using the robotic arm from ABB company, which confirmed the usefulness of the material for 3D printing, the material was applied to the full-scale 3D printer. The large-scale application showed some new problems. One of them was achieving the proper temperature for material hardening. In the 3D printing process, the material has relatively short time to achieve the required properties as compared to the traditional casting process. Time of hardening is important because of the interlayer bonding and its thickness. Particular properties of the final products could depend on the layer thickness in the 3D printing technology. The thin layers on a small scale blend faster than the thick ones on a large (industrial) scale. To achieve the required temperature, the test was conducted using a thermoactive camera (Figure 3). The results enabled to make some changes in the construction of the 3D printer, such as shortening of the hoses, and to achieve desirable results. Changes were based on the additional heat provided by infrared heaters. These changes enabled the material to cure faster from the outside and made printing easier.
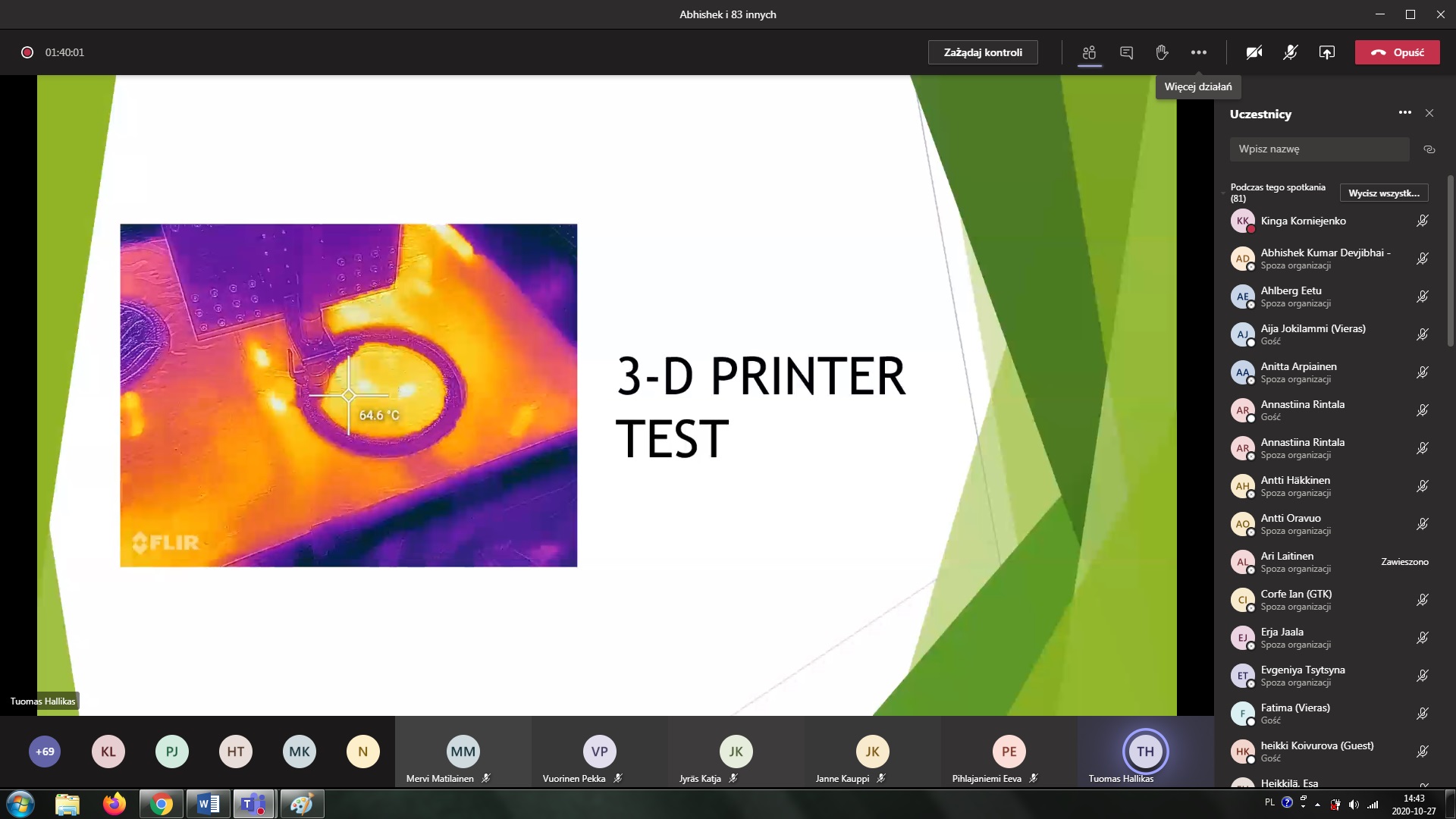
Another important factor is the pumpability of materials and their even distribution. The particular layer must not only have a proper strength for application to another layer in a short time, but it also must be reactive enough and in a ‘liquid’ state to properly blend with the previous layer. Some problems occurred when complicated shapes were printed. The equilibrium between speed and material distribution must be maintained. The main challenge at this stage is process stabilisation, including replicability of the manufactured elements to ensure process control for increasing the quality of the final products. The trials showed that the material behaviour in this area for geopolymers is completely different than that for traditional concrete. The problem was solved by making changes in charge pump and hose system. The distance between the pump and the print head was reduced. This step ensured that the printing head does not heat up and clog during the printing process. Additionally, two support systems were implemented. First, two devices for vibration were introduced. This improved the uniformity and pumpability of the mass. Second, the system of “pushing” the mass at the beginning and end of the process was implemented. This system was based on the use of compressed air. These changes ensured smoothness and efficiency of the process and enabled proper printing of complicated shapes.
Presently, the work on scaling up the 3D printing technology for geopolymers is in progress, and the planned construction work should start shortly. Most of the elements of the noise barrier (over 100 m length) have been successfully printed, and they are awaiting installation in the previously chosen place (Figures 4 and 5). The prototype solution (noise barrier) will be installed in the previously selected place near the school and the kindergarten. The sound-absorbing screen in this place will block the noise from railway trains.
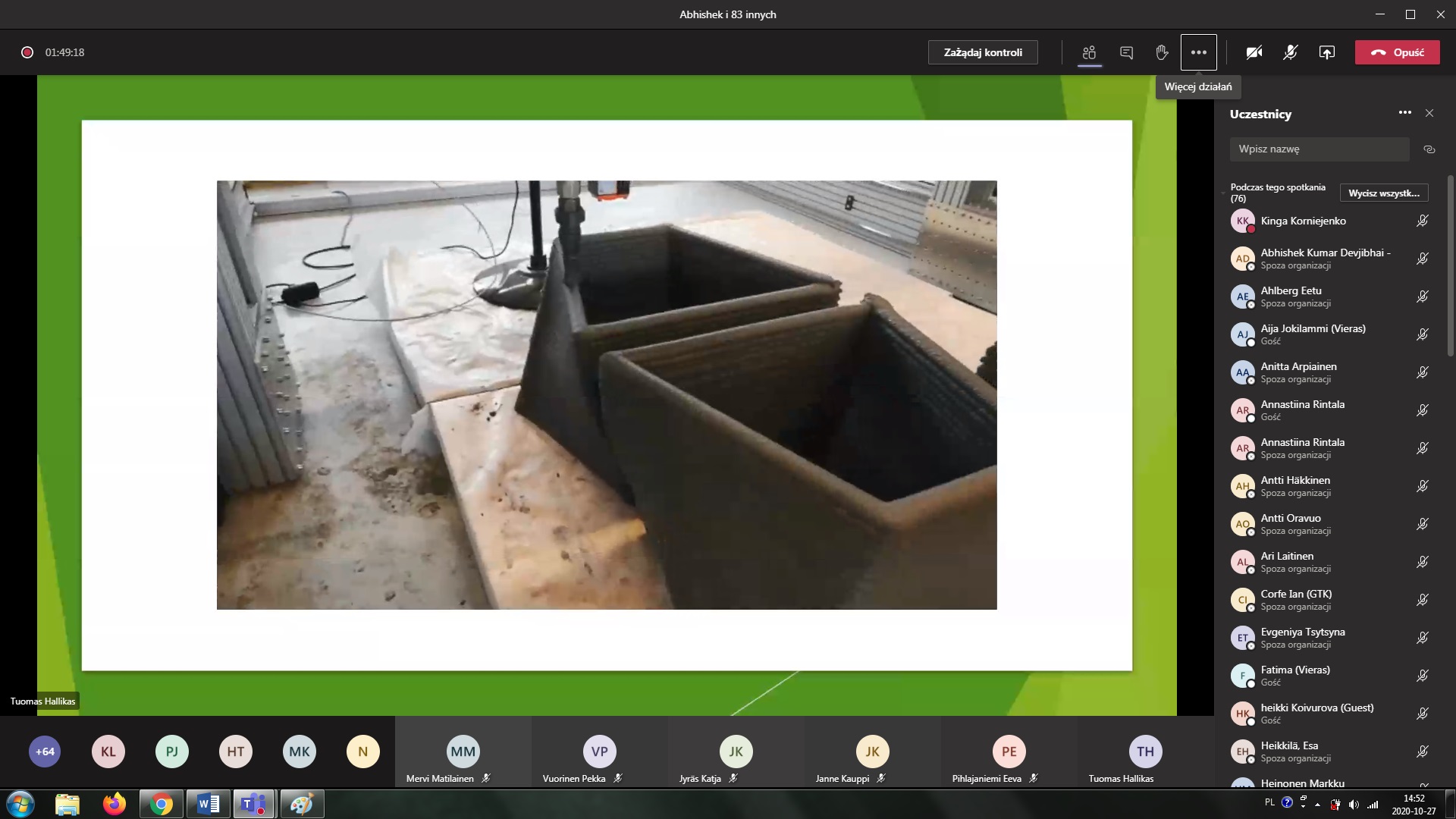
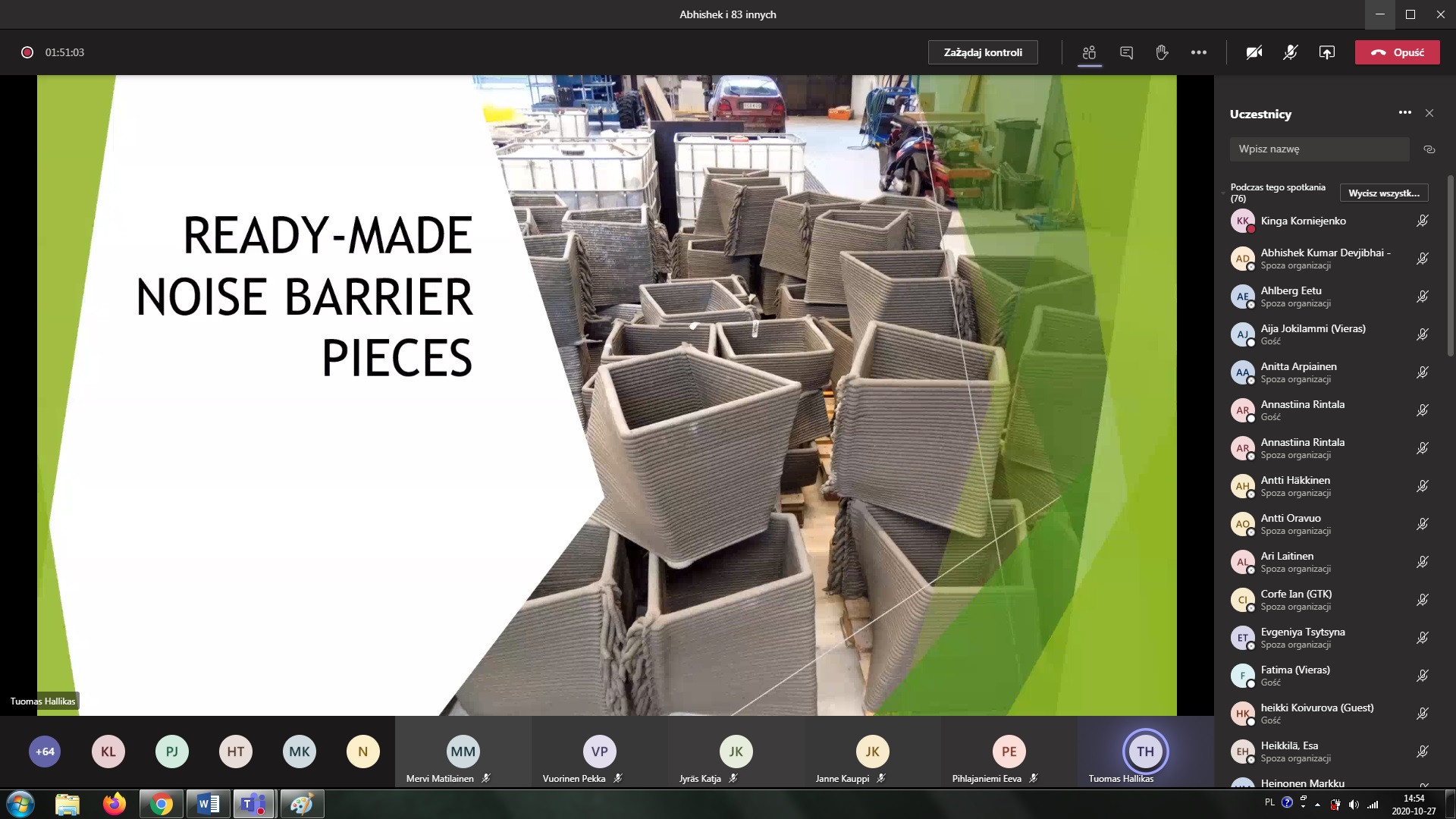
The project of the prototype solution give a possibility for using all the prepared recipes for different elements made with two different technologies: casting and additive manufacturing. Among the planned recipes, three are dedicated for traditional casting technology and two for modern additive manufacturing technology. The planned variants allow to compare optimal shape, technology, and material for future work and other applications for developing objects of small city architecture such as benches and pots.
The work is planned to be finalised in December 2020.
2. Implementation status
In the last period, the management was very effective. It comprised a project leader from the city of Lappeenranta and a Steering Committee for support. The main role of the city of Lappeenranta was supervising and coordinating the activities and tasks. The Steering Committee included the representatives of the key partners. It effectively support the leader in key activities, including implementation and communication activities. The leadership was quite challenging because of large size of consortium and COVID-19 pandemic. Despite the situation, the project was managed very smoothly at each level by the leadership. Because of the COVID-19 pandemic, many tasks were performed using online tools. The supporting IT system have been implemented since the beginning of the project, but there usage was crucial in the recent period.
At the operational level, regular meetings were conducted using web meeting platforms such as MS Teams. The on-line video connection helps with better understanding each other. Moreover the project coordinator try to ensure that all partners have the same level of understanding of the project during the individual meetings. This management approach helped to receive proper feedback from the partners and to achieve better communication with them.
Public procurements were completed in the first stage of the project. They were fully in line with the procedures presented in grant application. The procedures were performed in a traditional way. The public procurement procedures for the project were successfully completed without any problem.
Albeit the particular departments of the city of Lappeenranta collaborate mainly through online tools, this approach is very effective. The cross-departmental cooperation is supported by virtual meetings. It includes not only the decision-making process but also common activities related to project finalisation. The realisation of the prototype requires inter-departmental collaboration and some consensus in the final stage of the project.
The project activities are designed using a participative approach. Despite a large number of the participating organisations from different sectors, which play different roles in the project, the communication between the consortium members is excellent, and they actively participate in the decisions taken by the consortium. Cooperation between the companies and public organisations is well developed. Each partner can influence the consortium’s decisions, and during meetings, their opinion are considered. This helps to create better and more effective solutions. The participative approach is supported by regular meetings between the partners and the project leader with openness to ideas. The city cares about each organisation's point of view. The consortium members have an opportunity to open dialogue during formal meetings with all consortium members and to conduct informal meetings between smaller groups of partners. Presently, the communication is mainly provided by the Internet using a web-based platform and dedicated software for the project.
The size of the consortium makes it challenging for monitoring and evaluation tasks. Monitoring and evaluation are performed by the city of Lappeenranta. These tasks are supported by an indicator-based system to monitor and measure the project’s progress and task compliance. Monitoring and evaluation are based on the indicators described in the grant application. The project status is checked regularly, and the necessary data are updated. The collective database is very helpful in this area. The consortium members have online access to the newest data. The absence of proper indicators warns of potential problems and delays in the project. The last period required some changes in the monitoring system because the schedule of the project was slightly updated – extended up to December 2020. Monitoring and evaluation are the most important aspects in the last months of the project. During this time, the indicators will be verified again and benchmarked against best practice standards.
The planned objectives for communicating with target beneficiaries are achieved. The communication campaign was well coordinated and successful. The most important event in the last period was presented during the conference titled “Construction revolution begins in South Karelia - Urban Infra Revolution”. The conference was held online on 27 October 2020. The consortium decided for the online platform because of the situation related to the COVID-19 pandemic. The conference has been recorded, and the information will be accessible shortly. The presentation was focused not only on the progress of the project, but it also provided professional information on designing of new technologies in city planning and 3D-printed geopolymer materials in construction technology. The open platform and a wide range of up-to-date topics encouraged many people to participate. There were regularly more than 70 persons during the sessions. The invited guest – futurist Elina Hiltunen – presented the topic related to future megatrends in the circular economy. Her presentation helped to understand the significance of the project for the development of the entire region. It is worthy to mention that Elina Hiltunen is one of the top speakers in Finland in this area (best-seller speaker in Puhujatori, Spring 2020) and is also on the list of top 25 women futurists in the world. Her attendance motivated many people to participate in this event.
In addition to the conference, other activities related to communication with target beneficiaries were conducted. In the last period, the activities were focused on the Internet. In addition to the official UIA project’s website that is accessible in English and French, the information was also published on the website of the city of Lappeenranta, which is linked to eco-friendly solution applied in the city - it is accessible in English and Finnish. Additionally, some specific events were announced on the websites of all project partners and in Finnish info-portals.
Two initiatives were particularly interesting. The first one is associated with the presentation of a 3D model of the city centre of Lappeenranta to the public during the Greenreality Carnival. The model has also been published online and can be viewed in the Mapgets platform. The model presents a plan of the city of Lappeenranta in 2050. The 3D city model is a part of the UIR project, and it considers the results of the project (Figure 6).
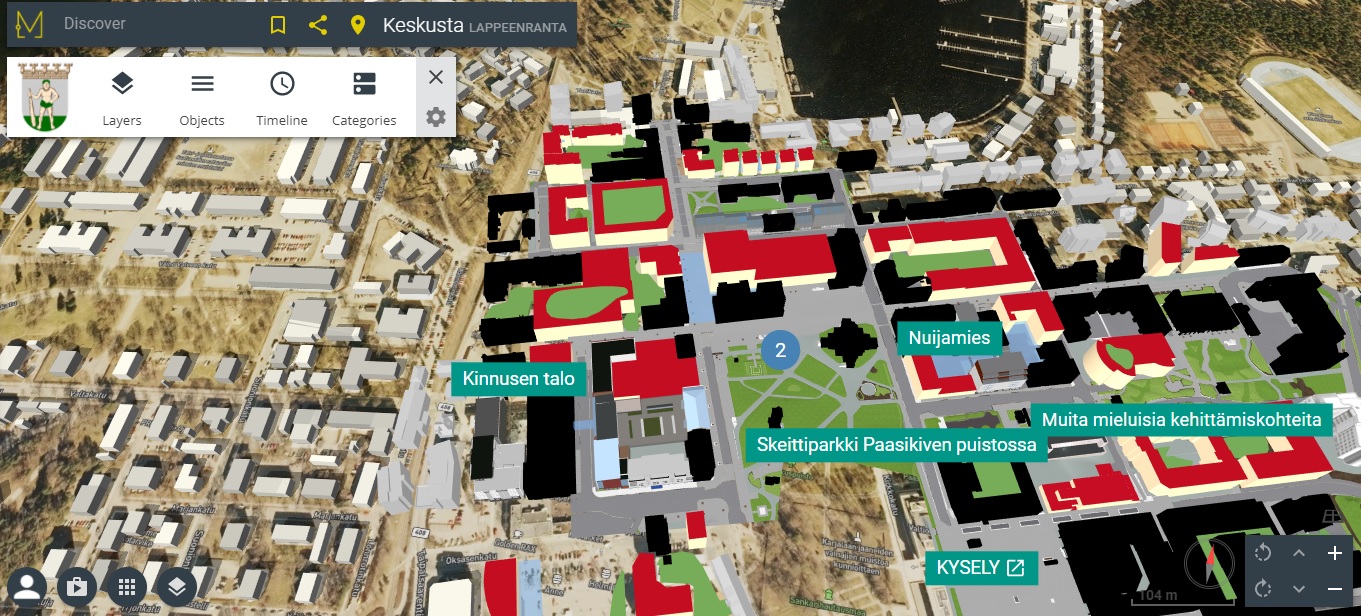
The second important event during the last period was that the city of Lappeenranta (Finland) won the title of the greenest city in Europe, European Green Leaf Award 2021, in a competition organised by the European Commission. The project activities partly contributed to this success.
Currently, upscaling remains the main challenge in the project. The COVID-19 pandemic situation has delayed the finalisation of the production and start of construction works. The project has been extended to the end of 2020, and some works associated with upscaling are still being continued. At present, the progress is significant. The full-scale model of the 3D printer has been construed and tested. The test results indicated some problems, and additional construction works were needed, such as changes in pumping systems and implementation of an additional heating system (please see section 3.2). After making these changes, the production of elements for the noise wall has started. Currently, most of the elements are ready to install in the noise wall, and it seems that the project will be completed on time.
Table 1 summarises the implementation challenges for the UIR project. The main areas are grouped in seven thematic areas. According to the risk level, the challenging areas are marked as follows: red: high risk and important for the project, yellow: medium risk and important, and green: low risk and important or the tasks in the area were successfully completed.
3. Project Challenge
The leadership and coordination are managed by the city of Lappeenranta. The leadership has a participative style with taking into consideration the opinions of all partners. It is consistent and accepted by all partners. The city organises regular meetings where all problems are discussed and further plans are presented. In the last period, the communication was performed using modern technology such as web-based platforms. The consortium used modern ways of communication during the entire project (communication through the Internet and sharing files on a common server); because of this adaptation, restrictions concerning the COVID-19 pandemic situation were smoothly implemented.
The public procurement procedures planned for the project have been successfully completed. The procurement procedure was organised in a traditional way; no innovative methods of procurements were applied in the project.
The cross-departmental communication in the city was efficient. The departments collaborated with each other. The city has also established good working relationships between the involved departments. In the last period, internal cross-departmental working was conducted mainly through the Internet. One of the valuable results from cross-departmental working was the design of the software that presents a plan of the city of Lappeenranta in the year 2050. Various project participants worked cooperatively to create a vision for Lappeenranta in 2050, including different departments of the city of Lappeenranta. This collaboration did not cause any complications, and the results were timely delivered by particular units. The results are accessible through the webpage of Greenreality.
The consortium is characterised by very effective collaboration mechanisms that involves all partners. The consortium members know their role and support each other. They fully understand the situation related to the implementation of restrictions for the COVID-19 pandemic. The consortium members communicated mainly through the Internet and made phone calls in urgent situations.
The monitoring and evaluation procedures are properly designed and effectively implemented. The problems and delays in the project are reported, and proper actions are taken, including monitoring the risks associated with changeable law (restrictions for the COVID-19 pandemic). The information on the current status of the project is properly disseminated to all partners. Nevertheless, for proper functioning, this area requires special attention during the last few months of the project. Particular activities should be undertaken to re-analyse all project documentation and achieved progress, especially objectives, milestones and outcomes.
Communication with target beneficiaries is a very important aspect for successful outcomes of the UIR project. The communication campaign is well coordinated and successfully implemented. It is a strength of the project. The consortium paid utmost attention in communicating activities. Because of the COVID-19 pandemic, most of the communication activities are being conducted through the Internet by using necessary software.
The good practice, from the last period, was the activity associated with the creation of a model that presents a plan of Lappeenranta in 2050. This activity was aimed not only to create an attractive tool for promotion but also to use it for communication with citizens. 3D modelling makes it easier for people to understand and comment on planned developments. The 3D model is accompanied by a survey to allow people to provide feedback on topical areas in the city centre. The survey focuses on concrete and current topics for the citizens of Lappeenranta and is accessible through the website in Finnish language.
During the last months of the project, the most important challenges are associated with upscaling of the technology. The preparation of the prototype is in progress.
The deadline has been changed, and all works need to be completed before December 2020. Milestones are being achieved according to the new schedule. The most important milestones in the previous period were construction of the large-scale 3D printer and start of production of the elements for the noise barrier. At present, the situation seems to be good and the new schedule is realistic.
4. Main lessons learned
From March 2020 to end of October 2020, the significant progress in Urban Infra Revolution (UIR) project was made. The two work packages are almost finished (the planned realization of the project is up to end of 2020). Work Package no. 6 Piloting was connected with a creating a vision of “urban city 2050”. The main goal of this Work Package was achieved by the creating the Mapgets platform. Using a augmented reality technology the model of the city of Lappeenranta in 2050 is presented. The layers in this models allows following to the predicted city development between 2020 and 2050. The 3D city model was created by collaboration of designers, policy-makers, citizens and other participants of the project (more information about this particular aspect of the project is presented in Zoom-in no. 3).
The Work Package no. 7 is almost ended. The city of Lappeenranta in cooperation with companies engaged in the project is discussing the best way for market potential upscaling of the solution developed in the project. The topic of the discussion is not only practical usage of the project and the technology but the creating the circular economy based on the project experience. For this purpose the involvement the local companies is crucially important. During the project the cooperation between the local companies was a main factor of the success. On the one side they deliver the products such as UPM, Nordkalk or Outotec company, develop the process – Apila Group and technology Fimatec. The local business is also the main target group for the long-term benefits from the project outputs.
Nowadays, the most important issue for the project is successful ending of the prototype noise wall till the end of December 2020. in the meantime, they are equally important activities are support the local business during the crisis caused by pandemic and acceleration of implementation the project outputs, including the usage of secondary raw materials as a product for the local companies. This topic was also discussed during the final conference: “Construction revolution begins in South Karelia - Urban Infra Revolution” on 27 October 2020.
Conclusions and next steps
The article summarises the most important activities that occurred in the last months in the UIR project. In this period, the work associated with scaling up of the technology was particularly important. A significant progress in the project was achieved in these areas. This brings good prospects for the future and successful projections for the completion of the UIR project in December 2020. Most of the technical problems have been overcome, and the project is in the last phase of implementation.
There is still a question of using the developed solution on a wider scale. The application of the local waste or by-products, in the technology, brings large benefits for the environment, but it also caused some challenges in scaling up the solution at the international level. The technology is dependent on chemical and mineralogical composition of the raw materials (local waste or by-product resources). This caused some limitations for using them in other regions and other countries with different industrials sectors. A potential user must be aware that the use of this technology will require some changes in the system because of a new composition of raw materials.
The article summarises the most important activities that occurred in the last months in the UIR project. In this period, the work associated with scaling up of the technology was particularly important. A significant progress in the project was achieved in these areas. This brings good prospects for the future and successful projections for the completion of the UIR project in December 2020. Most of the technical problems have been overcome, and the project is in the last phase of implementation.
There is still a question of using the developed solution on a wider scale. The application of the local waste or by-products, in the technology, brings large benefits for the environment, but it also caused some challenges in scaling up the solution at the international level. The technology is dependent on chemical and mineralogical composition of the raw materials (local waste or by-product resources). This caused some limitations for using them in other regions and other countries with different industrials sectors. A potential user must be aware that the use of this technology will require some changes in the system because of a new composition of raw materials.
About this resource
The Urban Innovative Actions (UIA) is a European Union initiative that provided funding to urban areas across Europe to test new and unproven solutions to urban challenges. The initiative had a total ERDF budget of €372 million for 2014-2020.
Similar content
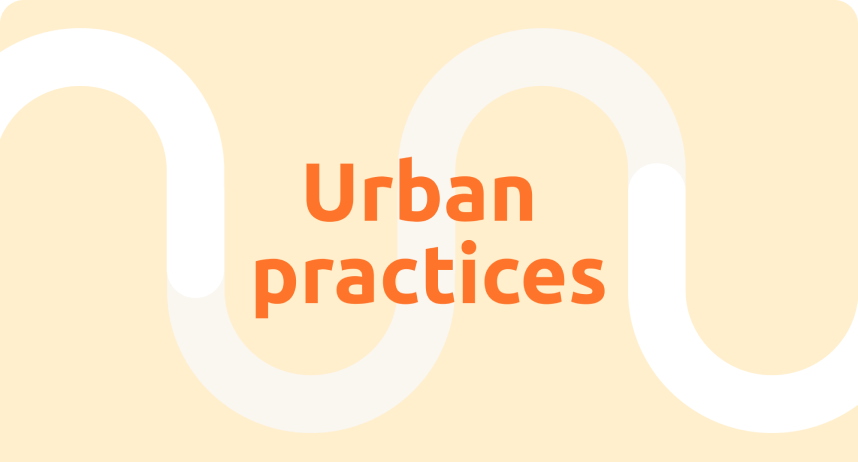
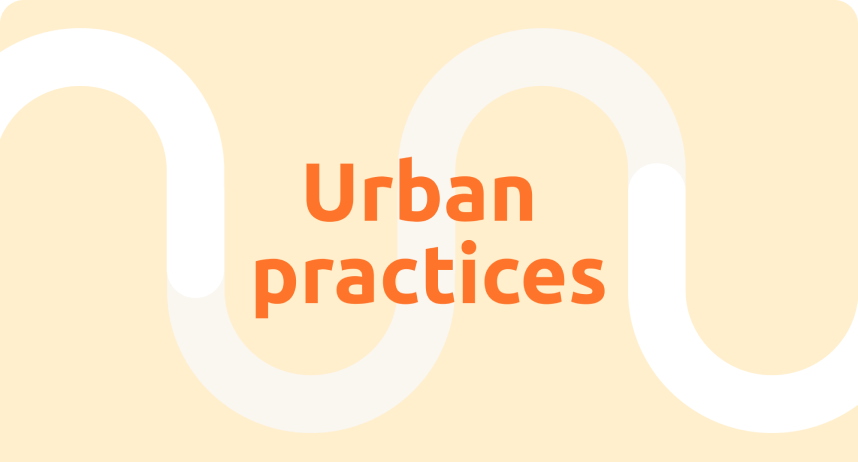
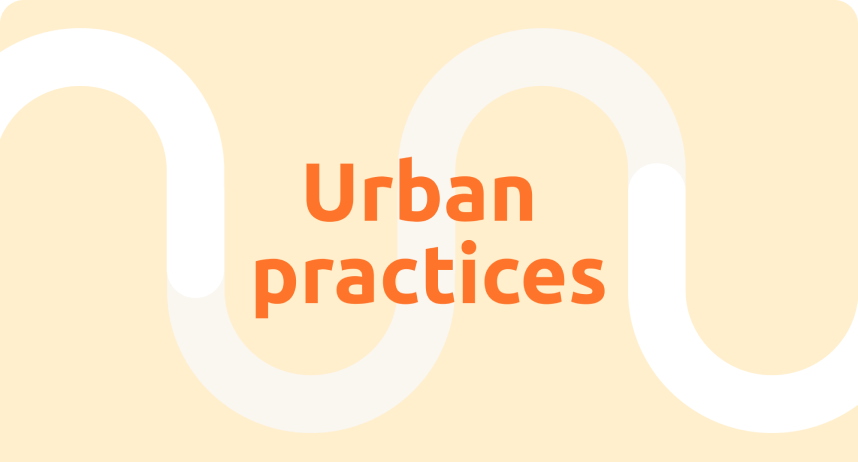