Do we need innovations? 3D printing technology for construction materials - ZOOM IN 2
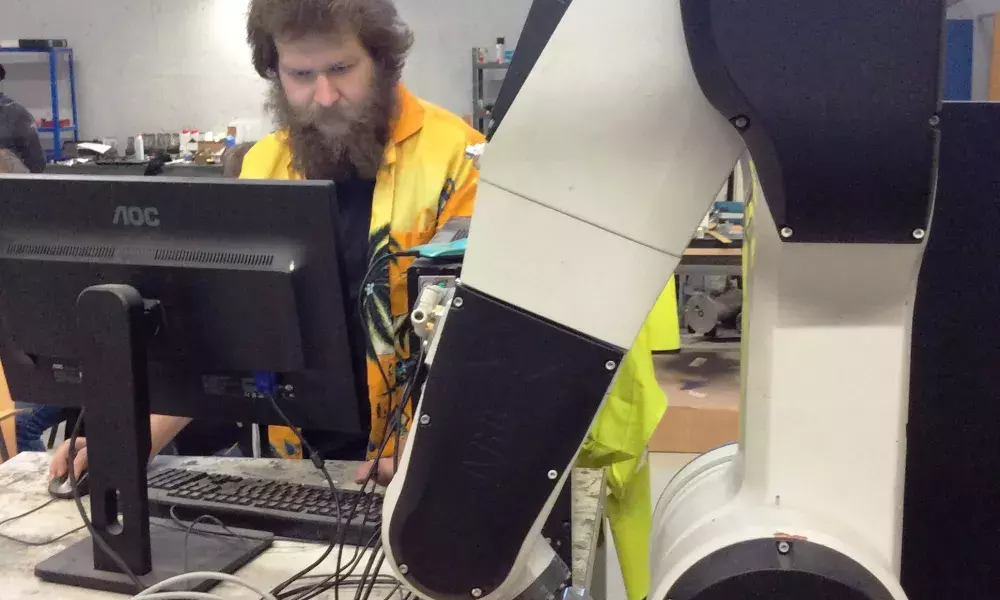
The main purpose of the Urban Infra Revolution and the City of Lappeenranta is to develop 3D printing processes to achieve finished components for construction industry with reduced life cycle costs. The innovation itself is the possibility to create the first manufacturing method that demonstrates fully closed loop construction: on-site built, local waste based and fully recyclable construction materials.
Three dimensional printing (3D printing or 3DP), called also as additive manufacturing, is the way of manufacturing by creating a 3D solid object from a digital model by building layers. This technology becomes more and more popular in different areas of the human activity, such as automotive, medicine, education etc.
The main innovation of this technology is connected with a new approach to production process. It could be slightly different for each type of 3D printing process. The first stage is producing a 3D model using CAD software. This model could be designed with 3D scanning, invented by designer or based on other project. The next stage is conversion to the standard tessellation language (STL) format. Most 3D printers use STL files. Next, the file is transferred to the computer that controls the 3D printer. At this moment, it is possible to make some changes in the object, by setting-up the device, such as size. After that, the process is starting. The 3D printer should be checked regularly during this time to make sure that there are no errors. After the process is finished, the printed object is removed from the device. The last step is post-processing, for example brushing off any remaining powder or curing.
The whole manufacturing process could be different, because different techniques are applicable in 3D printing. According to ASTM (the American Society for Testing and Materials) standard there are seven categories of additive manufacturing:
- Vat Photopolymerisation, including Stereolithography (SLA), Digital Light Processing (DLP) and Continuous Liquid Interface Production (CLIP),
- Material Jetting,
- Binder Jetting,
- Material Extrusion, including Fused Deposition Modeling (FDM) and Fused Filament Fabrication (FFF),
- Powder Bed Fusion, including Multi Jet Fusion (MJF), Selective Laser Sintering (SLS) and Direct Metal Laser Sintering (DMLS),
- Sheet Lamination,
- Directed Energy Deposition.
In case of construction industry three of them are applicable:
- material extrusion for different materials: concrete/cement, wax, foam, polymers,
- powder bed fusion, called also powder bonding for polymer bond, reactive bond, sintering,
- additive welding.
Material extrusion is nowadays the most applied technique. In that technology, the material is extruded from a nozzle mounted on a gantry to print a structure layer by layer.
3D printing is a rapidly developing industrial sector and potentially a disruptive technology. This technology brings new advantages such as resources saving and is more energy effective and sustainable compared to subtractive technologies. The technology has a huge potential to disrupt the way in which a product is designed, developed and manufactured.
In traditional industry, the design and development of the product is a responsibility of industry designer. The large series of the same products are manufactured. Nowadays, it has changed - the design and development of the product in case of 3D printing could be made by user. The design has been disconnected from the manufacturing process. A customer could make a project himself or buy it from a designer and perform it on own 3D printer (or subcontract it to someone else). The product can be easily customized without additional costs.
The disruptive element is also an effectiveness of the manufacturing process, especially possibility of low cost manufacturing for short series of the products. This technology allows simply customization of the products. It could be adjusted to individual requirements. In the case of 3D printing short series are preferable and the traditional industrial plants are no longer required.
Today, 3D printing in construction industry becomes more and more popular[1], [2]. It has a lot of potential advantages for construction application and can provide new horizons in this sector, such as increasing geometrical flexibility, reduction of labour costs, improvement of efficiency and safety, construction in harsh environments and sustainability[3], [4].
The most important element of this technology is geometrical flexibility. It allows to improve creativity and develop architectural expression, especially, because the cost of producing a structural component is independent of the shape. It gives more possibilities of creating new forms and shapes. It guarantees freedom of design and creation of curvilinear forms. These shapes allow not only for a more complex geometry and the aesthetic designing, but also they are structurally stronger than traditional ones. Stress concentration is lower and less material must be used. Optimized topologies allow for cost reduction[5]. Moreover, 3D printing makes it easier to produce individually designed elements for the same price as the ‘standard’ one . It could be a chance to develop the products according to specific needs, for example for disabled people (residential houses created for their needs).
The important element is also a reduction of costs, especially connected with manpower involvement in production process. 3D printing supports automation of building products manufacturing, including the possibility of ‘producing whole houses’. The other important factor is improvement of efficiency and safety. This technology is more cost-effective, offer high-precision and low-unit on-demand manufacturing in comparison with traditional one[6]. In the traditional construction technology a lot of additional elements are necessary such as forms or shutterings. 3D printing reduce the necessity of formwork[7] that is one of the most laborious elements in traditional construction industry.
Another benefit from using additive manufacturing is possibility of construction in harsh environments like sub-arctic clime of Finland. It is connected with possibilities of significant automation of production process. In this kind of environment additional problems with material occurred, especially with binding process, but perspectives are very promising. This kind of solution has been tested even for in-space application for settlers on Moon[8], [9].
Nowadays, the sustainability of the technology became one of the most important factor. 3D printing technology not only uses less material by effective design, but also reduces wastes, such as previously mentioned construction wastage of formwork - less material is used for moulding and casting operations.. It reduces environmental influence of the technology as well as costs of performance. 3D printing technology also reduces the carbon footprint through minimizing inefficiencies during building process[10]. The replacement off-site manufacturing, transportation of materials, installation and assembly, and on-site construction by on-site manufacturing using local raw materials minimizes greenhouse gases emission and save the energy[11]. As a result, the carbon footprint left by 3D printing technology is lower than one that is left by traditional construction technologies[12].
[1] J.G. Sanjayan, B. Nematollahi, M. Xia, T. Marchment, Effect of surface moisture on inter-layer strength of 3D printed concrete, Constr. Build. Mater. 172 (2018) 468–475.
[2] N. Labonnote, A. Rønnquist, B. Manum, P. Rüther, Additive construction: State-of-the-art, challenges and opportunities, Automat. Constr. 72 (2016) 347–366.
[3] B. Panda, M.J. Tan, Rheological behavior of high volume fly ash mixtures containing micro silica for digital construction application, Mater. Lett. 237 (2019) 348–351.
[4] D.G. Soltan, V.C. Li, A self-reinforced cementitious composite for building-scale 3D printing, Cement Concrete Comp. 90 (2018) 1-13.
[5] M. Xia, J. Sanjayan, Method of formulating geopolymer for 3D printing for construction applications. Materials and Design 110 (2016) 382–390.
[6] N. Labonnote, A. Rønnquist, B. Manum, P. Rüther, Additive construction: State-of-the-art, challenges and opportunities, Automat. Constr. 72 (2016) 347–366.
[7] M. Xia, J. Sanjayan, Method of formulating geopolymer for 3D printing for construction applications. Materials and Design 110 (2016) 382–390.
[8] C. Montes, K. Broussard, M. Gongre, N. Simicevic, J. Mejia, J. Tham, E. Allouche, G. Davis, Evaluation of lunar regolith geopolymer binder as a radioactive shielding material for space exploration applications, Advances in Space Research 56/6 (2015) 1212-1221.
[9] G. Davis, C.Montes, S. Eklund, Preparation of Lunar Regolith Based Geopolymer Cement Under Heat and Vacuum, Advances in Space Research 59 (2017).
[10] M. Xia, J. Sanjayan, Method of formulating geopolymer for 3D printing for construction applications. Materials and Design 110 (2016) 382–390.
[11] D.G. Soltan, V.C. Li, A self-reinforced cementitious composite for building-scale 3D printing, Cement Concrete Comp. 90 (2018) 1-13.
[12] C. Achillas, D. Aidonis, E. Iakovou, M. Thymianidis, D. Tzetzis, A methodological framework for the inclusion of modern additive manufacturing into the production portfolio of a focused factory, J. Manuf. Syst. 37 (2015) 328–339.
3D printing can provide new horizons in the construction sector, . Unfortunately, the full exploitation of 3D printing in construction industry is currently limited due to the in-process and in-service performance of the available materials.
Currently, the most important challenges for 3D printing technology in construction industry are innovative materials; this materials should have a good combination of all essential material properties[1]. These challenges are connected with new materials development, including geopolymers for 3D printing in the large-format printer. This material offers a new perspective for construction industry, but development of this technology is slowed down by a lot of barriers. Literature gives a lot of other required parameters for that kind of material, including[2], [3]:
- pumpability - reliability with which material is moved through the delivery system,
- extrudability - depositing material through a deposition device,
- buildability - resistance of wet material to deformation under loads,
- open time - period during which the aforementioned properties remain consistently within acceptable tolerance,
- thixotropic properties (high yield strength and low viscosity behaviour),
- short time of curing and possibility of curing in low temperature,
- interlayer bonding and segregation prevention,
- durability,
- ductility,
- vapour imperviousness,
- high tensile and compressive strength,
- low coefficient of thermal expansion,
- resistance to UV light.
The additional challenge is connected with post-processing procedures. The proper procedures could significantly increase geopolymer properties, but are hard for practical application, especially temperature that significantly increases mechanical properties of this material[4].
Other challenge in this area is using waste products such as clay bricks or mining tails as a raw material. A lot of mineral deposits in Europe are mostly depleted and, due to economic growth, construction and demolition waste (CDW) it has become a serious problem. In the EU, CDW accounts for approximately 25% - 30% of all generated waste, and it consists of numerous materials. Many of them can be recycled. The EC Waste Directive says, in Art 11- 2b, that: "by 2020, the preparing for re-use, recycling and other material recovery, including backfilling operations using waste to substitute other materials, of non-hazardous construction and demolition waste excluding naturally occurring material (...) shall be increased to a minimum of 70 % by weight." Using this kind of raw material for the 3D printing process in construction industry can bring a lot of environmental benefits, but it is also a challenge because of changeable material characteristic. The unstable chemical composition can cause problems with the process stabilization. It could also influence on final product’s properties.
[1] A.V. Rahul, M. Santhanam, H. Meena, Z. Ghani, 3D printable concrete: Mixture design and test methods, Cement Concrete Comp. 97 (2019) 13–23.
[2] N. Labonnote, A. Rønnquist, B. Manum, P. Rüther, Additive construction: State-of-the-art, challenges and opportunities, Automat. Constr. 72 (2016) 347–366.
[3] B. Panda, C. Unluer, M.J. Tan, Investigation of the rheology and strength of geopolymer mixtures for
extrusion-based 3D printing, Cement Concrete Comp. 94 (2018) 307–314.
[4] M. Xia, J.G. Sanjayan, Methods of enhancing strength of geopolymer produced from powder-based 3D printing process, Mater. Lett. 227 (2018) 281–283.
In comparison with traditional building materials, for example concrete, geopolymers have many advantages, but this material have also limitations. One of them, that hinder a wide use of this materials is their brittle behaviour and relatively low tensile and flexural strength. The reinforcement in the case of geopolymers is highly required because of limited brittle behaviour of these materials, especially cracks propagation under tensile and flexural loading[1]. Nowadays, one of the most important research areas is looking at improving its mechanical properties by reinforcing the matrix through fibres addition.
The challenge is to replace the conventional steel bars, well known from traditional concrete technology, with short fibres or long ones possible to apply in 3D printing[2]. The traditional reinforcement caused a lot of problems, such as the speed limitation and design limitations[3]. Additionally, their application can be also limited by technology of 3D printing requirements. A replacement could be made by steel fibres or alternative ones.
Hitherto, only few studies have been provided in the area of reinforced 3D printed composites by long and short fibres (Table 1.).
Table 1. Fibres used for reinforcement the 3D-printed geopolymer composites
|
Source of information |
Short fibres used in 3D printing technology |
|
Steel fibres |
S. Al-Qutaifi, A. Nazari, A. Bagheri, Mechanical properties of layered geopolymer structures applicable in concrete 3D-printing, Constr. Build. Mater. 176 (2018) 690–699. |
Glass fibres |
B. Panda, S.C. Paul, M.J. Tan, Anisotropic mechanical performance of 3D printed fiber reinforced sustainable construction material, Mater. Lett. 209 (2017) 146–149. |
Polypropylene fibres (PP)
|
B. Nematollahi, M. Xia, J. Sanjayan, P. Vijay, Effect of Type of Fiber on Inter-Layer Bond and Flexural Strengths of Extrusion-Based 3D Printed Geopolymer, Materials Science Forum 939 (2018) 155-162. B. Nematollahi, P. Vijay, J. Sanjayan, A. Nazari, M. Xia, V.N. Nerella, V. Mechtcherine, Effect of Polypropylene Fibre Addition on Properties of Geopolymers Made by 3D Printing for Digital Construction, Materials 11 (2018) 2352. |
Polyvinyl fibres (PVA)
|
B. Nematollahi, M. Xia, J. Sanjayan, P. Vijay, Effect of Type of Fiber on Inter-Layer Bond and Flexural Strengths of Extrusion-Based 3D Printed Geopolymer, Materials Science Forum 939 (2018) 155-162. S.H. Bong, B. Nematollahi, M. Xia, A. Nazari, J. Sanjayan, J. Pan, Properties of 3D-Printable Ductile Fibre-Reinforced Geopolymer Composite for Digital Construction Applications, in: V. Mechtcherine, K. Khayat, E. Secrieru (Eds.), Rheology and Processing of Construction Materials, RILEM Bookseries, vol 23, Springer, Cham, 2020, pp. 363–372. |
Polybenzoxazole fibres (PBO)
|
B. Nematollahi, M. Xia, J. Sanjayan, P. Vijay, Effect of Type of Fiber on Inter-Layer Bond and Flexural Strengths of Extrusion-Based 3D Printed Geopolymer, Materials Science Forum 939 (2018) 155-162. |
Flax fibres |
K. Korniejenko, M. Łach, S.-Y. Chou, W.-T. Lin, A. Cheng, M. Hebdowska-Krupa, S. Gądek, J. Mikuła, Mechanical Properties of Short Fiber-Reinforced Geopolymers Made by Casted and 3D Printing Methods: A Comparative Study, Materials 13 (2020) 579. K. Korniejenko, M. Łach, S. Y. Chou, W. T. Lin, J. Mikuła, D. Mierzwiński, A. Cheng, M. Hebda, A comparative study of mechanical properties of fly ash-based geopolymer made by casted and 3D printing methods, IOP Conference Series: Mat. Sci. & Eng. (2019) 660, 1-7. |
Carbon fibres |
K. Korniejenko, M. Łach, S.-Y. Chou, W.-T. Lin, A. Cheng, M. Hebdowska-Krupa, S. Gądek, J. Mikuła, Mechanical Properties of Short Fiber-Reinforced Geopolymers Made by Casted and 3D Printing Methods: A Comparative Study, Materials 13 (2020) 579. K. Korniejenko, M. Łach, S. Y. Chou, W. T. Lin, J. Mikuła, D. Mierzwiński, A. Cheng, M. Hebda, A comparative study of mechanical properties of fly ash-based geopolymer made by casted and 3D printing methods, IOP Conference Series: Mat. Sci. & Eng. (2019) 660, 1-7. |
Long fibres used in 3D printing technology |
|
Steel fibres |
J.H. Lim, B. Panda, Q.-C. Pham, Improving flexural characteristics of 3D printed geopolymer composites with in-process steel cable reinforcement, Constr. Build. Mater. 178 (2018) 32–41. |
Steel micro-cable
|
G. Ma, Z. Li, L. Wang, G. Bai, Micro-cable reinforced geopolymer composite for extrusion-based 3D printing, Mater. Lett. 235 (2019) 144–147. Z. Li, L. Wang, G. Ma, Mechanical improvement of continuous steel microcable reinforced geopolymer composites for 3D printing subjected to different loading conditions, Compos. Part B-Eng. 187 (2020) 107796. |
Aramid fibres
|
M. Łach, M. Hebdowska-Krupa, D. Mierzwiński, K. Korniejenko, Mechanical properties of geopolymers reinforced with carbon and aramid long fibers, IOP Conference Series: Mat. Sci. & Eng. (2019) 706, 1-8. |
Carbon fibres
|
M. Łach, M. Hebdowska-Krupa, D. Mierzwiński, K. Korniejenko, Mechanical properties of geopolymers reinforced with carbon and aramid long fibers, IOP Conference Series: Mat. Sci. & Eng. (2019) 706, 1-8. |
According to scientific knowledge the fibres addition caused:
- Increasing of flexural strength – for the samples with fibre addition it could be even 600% higher than for plain sample[4].
- improved inter-layer bonding, including influence of the time intervals between layer - reducing time gaps between additive layers and introducing fibres impact on the bond strength between subsequent layers[5].
- the fibres have negative influence on cracking propagation; they also reduce brittle behaviour of the geopolymers[6].
- short fibres as well as long ones are an effective way for reinforced the 3D printed geopolymers[7].
The fibre reinforcement of 3D printed geopolymers is a promising way to develop the materials for application in manufacturing on the larger scale in construction industry. This kind of composite can be a promising alternative for concrete in many applications and increases the freedom of design. It is particularly important in advanced architecture projects.
[1] D.G. Soltan, V.C. Li, A self-reinforced cementitious composite for building-scale 3D printing, Cement Concrete Comp. 90 (2018) 1-13.
[2] B. Zhu, J. Pan, B. Nematollahi, Z. Zhou, Y. Zhang, J. Sanjayan, Development of 3D printable engineered cementitious composites with ultra-high tensile ductility for digital construction, Materials and Design 181 (2019) 108088.
[3] B. Panda, S.C. Paul, L.J. Hui, Y.W.D. Tay, M.J Tan, Additive manufacturing of geopolymer for sustainable built environment, J.Clean. Prod. 167 (2017) 281-288.
[4] G. Ma, Z. Li, L. Wang, G. Bai, Micro-cable reinforced geopolymer composite for extrusion-based 3D printing, Mater. Lett. 235 (2019) 144–147.
[5] B. Nematollahi, M. Xia, J. Sanjayan, P. Vijay, Effect of Type of Fiber on Inter-Layer Bond and Flexural Strengths of Extrusion-Based 3D Printed Geopolymer, Materials Science Forum 939 (2018) 155-162.
[6] K. Korniejenko, M. Łach, S.-Y. Chou, W.-T. Lin, A. Cheng, M. Hebdowska-Krupa, S. Gądek, J. Mikuła, Mechanical Properties of Short Fiber-Reinforced Geopolymers Made by Casted and 3D Printing Methods: A Comparative Study, Materials 13 (2020) 579.
[7] M. Łach, M. Hebdowska-Krupa, D. Mierzwiński, K. Korniejenko, Mechanical properties of geopolymers reinforced with carbon and aramid long fibers, IOP Conference Series: Mat. Sci. & Eng. (2019) 706, 1-8.
For the Lappenranta city, all advantages connected with 3D printing are important, but the crucial are environmental benefits. The Infra Revolution project is the response for market and society needs, especially in the area of developing technologies for circular economy. It stresses the importance of using eco-friendly technologies. The main challenge is not only developing of zero-waste 3D printing technology, but also using waste products as a raw material and producing the prototype solutions for urban architecture. It significantly will help to achieve the ambitious goal of carbon free and waste free cities by reducing amount of unutilised waste from local industry and lowering CO2 emission. The project will contribute significantly to the reduction of CO2 emissions - 80% reduction of CO2 emissions from 2007 level to the target for 2030 and will completely eliminate waste - the target for 2050 (Fig. 1).
Project meeting – Lappeenranta as a green city
One of the expected results of the project is the design of new materials for additive manufacturing as well as modification of 3D printing process itself (extrusion based techniques). The project will demonstrate the ability of this processes to achieve finished components for construction industry with reduced life cycle costs. This composite should: close the loop of construction material, be applicable for extreme (arctic) weather conditions, be reinforced with biofibres and be based on local industry wastes. Using waste materials as a raw materials for 3D printing brings a lot of environmental benefits, but also it is a challenge[1]. Waste materials such as mining tails could strongly influence on 3D printing parameters and final product properties. Moreover, the research provided for one material are not applicable in a simple way to other one, for example the investigation on influence of the moisture on interlayer bonding shows that normally, existing water on the surface weakens a bond strength, but other found no influence of moisture condition on the bond strength[2].
The technique applied in the Infra Revolution project is extruder based 3D printing. The technology is developed by two steps. The first step – laboratory trials - were made in autumn 2019. For the test, a robotic arm, that holds a tube with material for 3D printing, has been used (Fig. 2). The material was extruded in controlled condition.
The process of development the 3D printing technology in laboratory
The second step is connected with scaling-up – development of industrial scale technology that will enhance the local industry business and accelerate the employment possibilities in circular economy. The material for prototype manufacturing has been prepared and the consortium is building a large scale 3D printer device (Fig. 3). The process will be also based on extruded technique.
The process of scaling-up the technology in the company Fimatec
In case of application, the technology in large scale the optimization of the material for 3D printing technology is required. The same material composition could have some properties in small (laboratory) scale and other in the large scale, especially: reactivity and stability. The other important factor is the speed of the printing. In 3D printing process the material has limited time to achieve required properties. The particular layer must have a proper strength to be applied to another one in short time, but it also must be enough reactive and ‘liquid’ to be properly joined with previous layer. The challenge is also the process stabilization, including replicability for the manufactured elements to ensure process control for increasing the quality of the final products.
[1] G. Ma, Z. Li, L. Wang, Printable properties of cementitious material containing copper tailings for extrusion based 3D printing, Constr. Build. Mater. 162 (2018) 613–627.
[2] B. Panda, S.C. Paul, N.A.N. Mohamed, Y.W.D. Tay, M.J. Tan, Measurement of tensile bond strength of 3D printed geopolymer mortar, Measurement 113 (2018) 108-116.
In case of using geopolymers for additive manufacturing technology, still, there is no successful implementation in industrial scale. The most advanced works are made by Russian company – RENCA. The company has designed 3D printer for geopolymers, create new material composition and construed the prototype. The technology was based on extrusion technique. It was tested in relevant environment. Recipes are individually created for each customer. More information: www.geobeton.ru and www.apis-cor.com.
Other solution is being developed by Chinese university. They mainly use printing from powder (using powder sintering). The long steel fibres are used as a reinforcement for that research. In this case some laboratory prototypes are developed[1], [2]. Other laboratory prototypes have been done by Swinburne University in Melbourne, Australia, KULeuven university (Belgium) and some other universities, but this solutions are on the very early stage.
[1] J.H. Lim, B. Panda, Q.-C. Pham, Improving flexural characteristics of 3D printed geopolymer composite with in-process steel cable reinforcement, Constr. & Building Mat. 178 (2018) 32-41.
[2] B. Panda, M.J. Tan, Experimental study on mix proportion and fresh properties of fly ash based geopolymer for 3D concrete printing, Ceramics International, 44 (2018) 10258-10265.
The main planned application is a noise wall. Currently the works on over 100 m length the noise barrier are in progress. The five different material compositions will be used for that construction. All recipes will use by-products from industry. Moreover, two different technologies are planned – 3D printing and traditional casting method. Three recipes are dedicated for traditional casting technology and two for modern, additive manufacturing technology (Fig. 4).
Visualisation on the noise barrier made by Design Reform’s plans of piloting products, source: Design Reform
Other planned products are elements of small architecture dedicated for citizens, especially pots and benches. These elements will be manufactured by 3D printing technology. It allows to receive more advanced forms and make the products more aesthetic. Public space is important for the Finnish people. They use it as a place of meeting and treat it as an important factor of standard life. These elements will be placed on main market, park around the castle and near to the schools. The last localization is especially important for citizens, because it will be a part of a social project defined as “friend bench”. This kind of bench will be used for socialization of the timid children. Each kid could sit on this bench and it will be a sign that this child would like to play with other kids. The last designed product is a skate park. In this case, the new technology has a lot of advantages. It allows novel functionality with more flexible and unique design in this kind of infrastructure. The idea of skate part is an initiative of local community (table 2).
Table 2. Basic data about using 3D printing technology in the project
|
Urban Infra Revolution - Circular economy materials and novel method development to produce recyclable and functional urban construction products |
Amount and sources of funding |
EU: co-financed by the European Regional Development Fund through the Urban Innovative Actions (UIA). Total project: 4 336 568.40 EUR Co-financing: 3 386 638.40 EUR |
Duration |
01/11/2017 - 31/10/2020 |
Consortium |
Lider: Municipal - City of Lappeentanta (Finland) Partners: 4 SME, 5 private enterprises, 2 universities, 1 Region Development Company |
Raw Materials |
Ashes, green liquor dregs, tailings, construction waste |
3D printing technology |
Laboratory (testing materials): Robotic arm; Scale-up: Large-format printer – printing inside the ready elements |
Planned product |
Noise wall, small architecture element such as pots and benches, skate park |
Conclusion
3D printing is a disruptive technology for the construction industry. This technology has many advantages such as resources saving, energy efficiency and friendliness towards environment. Currently, only few prototype applications for this technology have been developed. However, 3D printed geopolymers are a promising way to develop the materials for effective application in manufacturing on the larger scale, geopolymer composites still require development and optimization. The main challenge is connected with development innovative materials for construction purposes.
The technology of 3D printing for geopolymer composites brings low labour costs, less waste, and high efficiency. Unfortunately, their application is limited, only some prototype elements have been performed using this technology. The material - geopolymers still requires development and optimisation. The fibre reinforcement of the 3D printed geopolymers is a promising way to develop the materials for effective application in manufacturing on the larger scale. There could be a promising alternative for concrete in many application. The main purpose of the Infra Revolution project is developing 3D printing processes to achieve finished components for construction industry with reduced life cycle costs. The innovation itself is the possible first manufacturing method that demonstrates fully closed loop construction: on-site built, local waste based and fully recyclable construction materials. Currently, the consortium successfully developed laboratory small scale model based on robotic arm system and is working on large scale 3D printer.
About this resource
The Urban Innovative Actions (UIA) is a European Union initiative that provided funding to urban areas across Europe to test new and unproven solutions to urban challenges. The initiative had a total ERDF budget of €372 million for 2014-2020.
Similar content
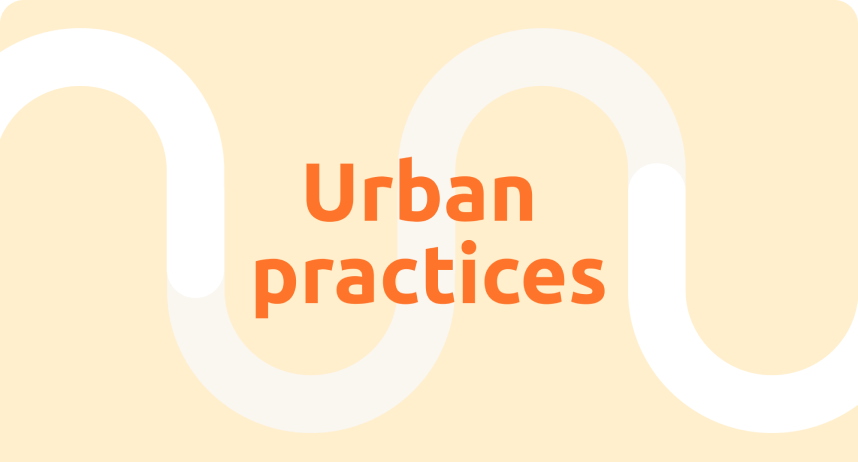
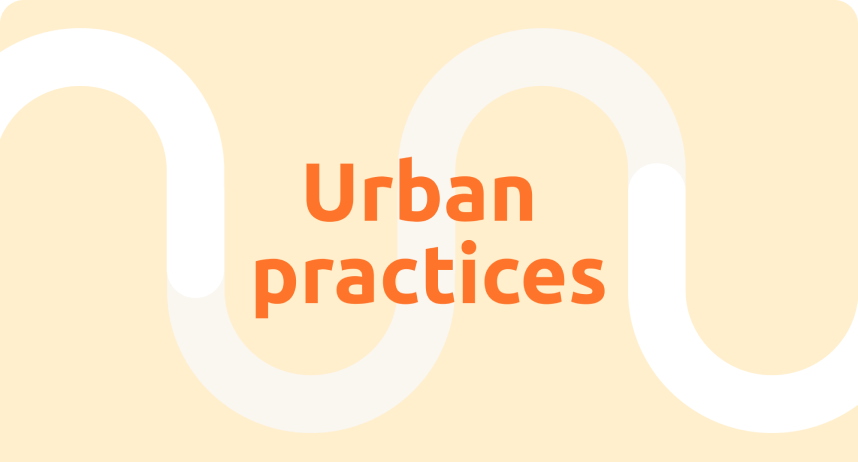
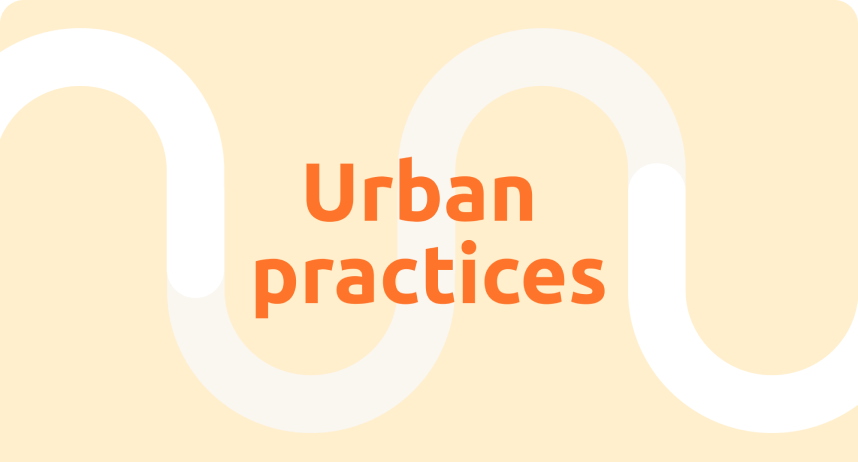