Super Circular Estate Project, Journal no. 5, Municipality of Kerkrade
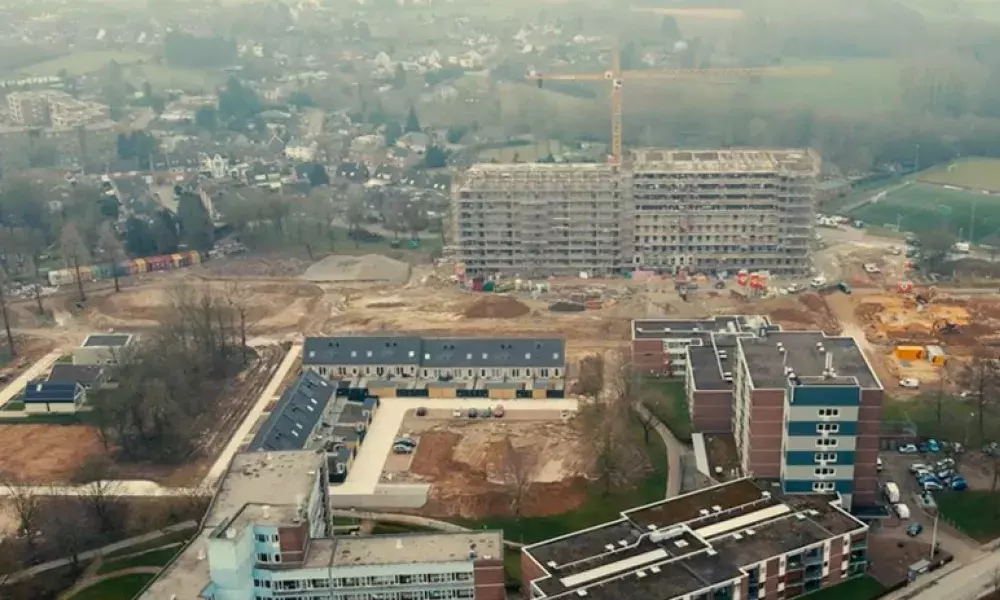
Number of solutions have been tested through the demonstration of circular concepts during deconstruction of 10-story flat building and construction of three new houses while reusing 95% of materials from a neighbouring downer building. These experiments illustrated potential of reactivating and extending material life at the end of building life by means of deconstruction and material/product reuse, demonstrating that end of building life does not necessarily mean end of materials life. Besides the demonstration of material circularity, several co-creation sessions with inhabitants have been organised, which resulted into their involvement into a physical transformation of the neighbourhood that brought about greater social interaction.
Last but not least, extraordinary step was made in the field of water recycling and creation of closed water cycles and water reuse systems in the neighbourhood and new housing.
This expert’s journal will elaborate on cost and benefits analyses as well as on lessons learned during the project and their implementation into a spin off projects. These helped to identify barriers and opportunities for the further evolution of construction industry towards a circular one.
The Super Circular Estate (SCE) project is one of the most frontrunning experiments on circular construction in Europe. The main objective of the SCE project was to investigate capacity of existing built environment to be activated as resource banks for new buildings. One of the key questions that the UIA Super Circular Estate project partners dealt with was “how to reverse building’s negative impact (associated with the end of building life on (i) social and (ii) environmental capital), into a positive one”?
According to the UN reports, urban agglomerations (neighbourhoods and cities) are responsible for around 65%of all energy used, 60% of all water consumed, and 70% of all greenhouse gases produced worldwide. Furthermore, 50% of total use of natural resources in Europe, 39% of material waste and 40% of total CO2 production is related to buildings. The exponential increase in population and contemporaneous increase in standard of living for many, will mean that the demand for essential goods & services (transportation, cars, housing, materials, water) will increase by at least a factor of 2 in the next few decades. It is through cities and vast urban agglomerations that mankind is increasingly present at the planet through which it mediates its relationship to the various stocks and flows of environmental capital. It becomes critical to understand the capabilities of urban areas to transform what is today a negative environmental impact to a positive one. The complex systemic and multi-scale capacities of urban areas provide great potential for a broad range of positive correlations with nature’s ecological / regenerative systems.
The Super Circular Estate project aimed to reverse the conventional approach to urban transformation (demolition and relocation of residents) into a circular approach, aiming at closing material circles within own restructuring area and at return of residents. Thus, the aim was reusing physical and social values as social and physical building blocks for the new construction and new neighbourhood. In the period of the last four years, the project explored the potential of circular management of resources including material, water and social circularity.
Number of solutions have been tested through the demonstration of circular concepts during deconstruction of 10-story flat building and construction of three new houses while reusing 95% of materials from a neighbouring downer building. These experiments illustrated potential of reactivating and extending material life at the end of building life by means of deconstruction and material/product reuse, demonstrating that end of building life does not necessarily mean end of materials life. Besides the demonstration of material circularity, several co-creation sessions with inhabitants have been organised, which resulted into their involvement into a physical transformation of the neighbourhood that brought about greater social interaction. Inhabitants became one of the important stakeholders during the urban transformation process enabling to reuse social capital that will take care of social continuity and cohesion of the neighbourhood in the future.
Last but not least, extraordinary step was made in the field of water recycling and creation of closed water cycles and water reuse systems in the neighbourhood and new housing.
All in all, SCE experiments illustrated potential of reactivation of resources within existing built environments and helped us understand better the balance/disbalance between costs and benefits of circular building concepts within a framework of the existing market and legal conditions.
This expert’s journal will elaborate on cost and benefits analyses as well as on lessons learned during the project and their implementation into a spin off projects. These helped to identify barriers and opportunities for the further evolution of construction industry towards a circular one.
Major challenges with respect to the difference between circular and conventional building process have been addressed by the SCE consortium members and elaborated in previous Expert’s journals and zoom-in movies (UIA Expert’s Journal 2019, 2020). Number of lessons learned have been presented in UIA Expert’s journal 4 and Zoom in no.3, as well as during opening of three SCE houses in Kerkrade and UIA SCE scientific conference “Crossing Boundaries” that took place in Heerlen on March 2021. As such, SCE results have already drawn attention of many Dutch and international research and industry groups dealing with circular economy in construction. During the last six months, results and findings from UIA SCE project were presented at:
- International scientific conference “Crossing Boundaries” March 2021, organised as a closing event of UIA SCE project by SCE partners ZUYD University, IBA and Region of Parkstad. (Figure 1)
- The project was nominated for International Guangzhou Award organised by, among others, World Association of the Major Metropolises (Metropolis), C40 Cities Climate Leadership and International Council for Local Environmental Initiatives. 273 sustainable building projects from 60 countries have been submitted. Super Circular Estate has been listed as one of 30 deserving cities and was included into a catalogue for the UN event on circular development. (Figure 1)
- Super Circular Estate is the winner of 'The Innovation in Politics Award 2020'.
- Project results and lessons learned have been presented to the EDA (beginning of 2021) and will be implemented in the recommendations to the French government by French demolition association.
Figure 1 : Presentation of results of SCE project and nominations for international awards
SCE project and implementation of circular building strategies into new applications
SCE consortium members addressed many challenges during the UIA SCE project, ranging from management of time and costs, change in deconstruction and construction culture and shifting of roles and responsibilities beyond the conventional path of design, engineer, construct, deconstruct. Lessons learned along this path resulted in couple of spin off projects, which will be elaborated in this fifth Expert’s Journal together with recommendations for future projects.
Figure 2: transformation area in Kerkrade for experiment on circular built environment before the UIA SCE project and transformational experiment
Faced with emerging trend in shrinking of the population and possible appearance of underperforming/abandoned areas due to a demographic change in Region of Parkstad, the Super Circular Estate project aimed to reverse the conventional approach to urban transformation (by demolition and relocation of residents) into a circular approach, aiming at closing material circles within own restructuring area while reusing physical and social values and using these as social and physical building blocks for the new construction. The project explored the potential of circular management for social housing association including material, water and social circularity.
In order to investigate possible solutions for future urban transformation projects in the region, municipality of Kerkrade (together with housing cooperation HeemWonen) specified a dedicated area in Kerkrade for the big scale experimentation. (Figure 2) This circular experimentation area was set up to address the urgent social and environmental challenge of both material and social circularity. The aim was to work on the circular transformation of the whole area together with its inhabitants and enable them to return to their neighbourhood once the transformation process has been finalised. This would enhance social and cultural continuity of the neighbourhood. To facilitate this process of social circularity, inhabitants were involved in co-creation sessions around the planning of the area, defining its shared spaces, landscaping, etc. Involvement of inhabitants helped also to get better view on general perception of users when it comes to reuse of materials and products and their general acceptance. Figure 3 shows overview of the experimental area dedicated by Municipality of Kerkrade and housing cooperation HeemWonen for circular deconstruction and construction experimentation. The area has been developed in four phases and UIA SCE circular houses project was one of them.
Figure 3: Transformation area in the last phase of circular experiment.
After four years of experimentation, the area has been transformed from an average housing area to an inspirational space that attracts many to visit and get a glimpse of the future. The area itself had four major phases of the development (Figure 3) starting with the:
(i) expo pavilion as preparation for the UIA project; (ii) then construction of UIA SCE three circular houses together with setting up of the infrastructure for water recycling (as joint effort of UIA and Life project); (iii) building additional 15 houses based on the lessons learned from the three UIA SCE houses; and (iv) refurbishing half of the last remaining 10-story block along with construction of the second half while implementing circular construction strategies and visions developed during the UIA SCE project. (Figure 3)
UIA SCE experimental phase
Pre UIA SCE phase involved deconstruction of the first 10-story block and construction of a prototype / expo pavilion made of 100% reused elements from the existing building block. Based on that experiment consortium of 12 partners (Municipality of Kerkrade, Brunssum municipality, Landgraaf municipality, Stadsregio Parkstad Limburg, VolkerWessels Construction, Real Estate Development South and Dusseldorp Infra, Water Board Company Limburg, Limburg Drinking Water Company, IBA Parkstad B.V, Zuyd University of Applied Sciences, HeemWonen, Association of Demolition Contractors (VERAS)) has defined project proposal for the UIA Super Circular Estate Project.
After the UIA SCE project has been awarded to the project consortium a strategy has been developed for testing, developing and monitoring of each deconstruction and construction phase of UIA SCE three houses. Special focus has been given to monitoring of environmental and economic impacts of tested circular technologies and construction methods. Detailed analyses and results of the monitoring has been elaborated in pervious UIA SCE expert’s journals, as well as through UIA SCE expert’s Zoom in (Super Circular Estate - First Circular Social Housing Estate for 100% Material and Social Circularity | UIA - Urban Innovative Actions (uia-initiative.eu))
UIA SCE deconstruction and reuse strategies applied in three SCE houses
Figure 4: hoisting and two 3D units for the construction of two circular houses (Type A left and Type B middle). The structure for the third house (Type C) has been made of recycled concrete.
The aim of the construction of the three new houses was to construct them using at least 95% of reused materials that are re-sourced from the donor building. During their construction, the following circular techniques have been tested:
- foundation has been made out of circular concreate (aggregate and cement for the concrete which have been acquired by crushing the existing concreate structure. 7% of new cement has been added during production of concrete for the foundation)
- main loadbearing structure of the two houses has been directly reused from the existing building by cutting 3D concrete modules from the existing structure,
- main loadbearing structure of third house has been made of circular concreate (aggregate and cement for the concrete, only 5% of new cement has been added during production of concrete for the structural walls)
- partitioning walls have been directly reused from the exiting building as well as
- wooden frames for doors and kitchen cabinets have been directly reused and finally
- façade has been constructed out of (i) parts using crushed concrete pieces from the existing building (ii) brick cut off elements and (iii) recycled concrete (Figure 4 and 5)
Figure 5: traditional demolition linked to the production of recycled concreate on site resulted into construction of third house, using 95% of recycled aggregate while bigger parts of crushed concrete have been used as a façade of one of the houses.
Depending on deconstruction and reuse strategy the end of use life of the building can trigger restart of material life on different levels of building composition and create shorter material loops as for example direct reuse of concrete units figure 4 and longer material feedback loops as reuse of parts and production of circular concrete based on recycled aggregate figure 5.
Methodology assessing financial feasibility of different recovery and reuse strategies considering environmental impact, has been developed by student J.J.M. Zaad from Zuyd University of Applied science. Financial assessment of SCE is a result of mapping parameters determining construction costs (internal costs) and environmental impact of construction (external costs) as listed below.
The cost of a project (internal cost) consists of the following components:
• Man-hours
• Material
• Equipment
The environmental impact (external costs) consists of costs related to:
• Embodied energy saved
• CO2 emissions saved
• Residual value- future value of materials (J.J.M. Zaad 2019)
In order to be able to analyse costs and benefits of SCE project, a conventional construction of recently built social house “Plus Living” with similar typology and material composition has been taken as a reference project.
Regardless of the level of technical decomposition and recovery all reuse and recycling strategies tested during SCE project had better performance with respect to CO2 emissions, embodied energy and material savings, compared to conventional construction methods. (Table 1 and 2)
Table 1: external environmental costs/benefits analysis of reused unit from the flat and circular concrete compared with costs of conventional prefabricated concrete walls of reference PlusLiving house. (J.J.M. Zaad 2019)( M.Ritzen 2019)
Table 2: internal and external environmental costs/benefits analysis of three reuse strategies tested in SCE compared with costs of conventional masonry façade of reference PlusLiving house. (J.J.M. Zaad 2019)(M.Ritzen 2019)
Takeaways from deconstruction and reuse experiments
Experiments within the SCE project changed the conventional perception of the end of building life (Figure 4 and 5), illustrating that end of life of a building does not necessarily mean end of product and material life. On the contrary, end of building life can be seen as a “restart” of new life and diversion of building products and materials from landfill and downcycling.
Contrary to the conventional demolition process, which has only costs associated to it, circular deconstruction and reuse projects bring benefits into equation that needs to be balanced from project to project. (Figure 6)
Figure 6: cost benefits analysis and impact of design solution on environmental and economic costs (Durmisevic 2021)
According to the reports of M. Ritzen (2019) and J.J.M Zaad (2019), recovery of tunnel shaped 3D concrete module saved 34% of CO2, 34% of embodied energy and 95% of raw materials, compared to conventional construction with concrete, which consumes 100% of raw materials, energy and emits 100% of CO2. Regardless of economic impacts, which are not competitive with market conditions and financial models of linear construction today, the SCE project proved that every reuse strategy that has been tested during the project has environmental benefits compared to conventional construction.
During the construction period of three SCE houses (Figure 4), noteworthy results have been achieved, illustrating the potential of circular building construction grounded on the capacity of the existing building to be re-sourced for the new construction. The UIA SCE tested 8 different deconstruction and reuse strategies and developed methods of circular construction which enabled to reuse 95% of materials from a 10-story building of the experimental area. These findings and methods enabled to reactivated 1.380.000 ton of building materials, 2.330.000 GJ embodied in existing materials has been reused together with 287.000 CO2/ton. (The environmental impact has been calculated by the knowledge partner of the consortium – ZUYD University of Applied sciences, M.Ritzen)
Re-activation of material life after the end of building life, and its costs and benefits, has been tested on three levels of building technical decomposition: (i) building/unit, (ii) part/element, and (iii) material level (figure 7) illustrating the costs side of deconstruction and reuse linked to the three levels of technical building composition and ease of separating the levels as independent layers during deconstruction. The results of SCE illustrated direct relation between the way a building has been designed/assembled and its environmental and economic impact during deconstructions and reuse.
Figure 7: hierarchy of levels of technical deconstruction of a building with view on high value reuse (Durmisevic 2009)
For buildings that are designed for disassembly and with recovery and reuse of its products in mind, the higher level of technical deconstruction (higher number of independent physical layers) will result in higher environmental and economic performance during recovery and reuse stage.
Direct reuse of complete unit and systems, designed as reversible parts of the building with disassembly and high value recovery in mind, eliminates use of new materials as well as energy and CO2 emissions associated with their production and requires less complex deconstruction technics and less labour. Main conclusion of the EU H2020 “Buildings as Material Banks” project https://www.bamb2020.eu/wp-content/uploads/2019/03/20190228-BAMB-D14.pdf is that higher reversibility of the building results into lower environmental and economic costs. (Figure 8)
Figure 8: diagram summarising correlation between level of reversibility of a building and its environmental and economic impacts (Durmisevic BMAB 2019).
However, this advantage is reversed when it comes to buildings and its parts that are not designed with recovery and reuse in mind, (which is the case with most of existing buildings). The 10-story flat building in Kerkrade is one of them. Figure 8 illustrates the comparison of two types of buildings (i) designed for demolition and (ii) designed for disassembly with LCC and LCA calculations. The higher disassembly potential/ reversibility of building, the lower the LCA and LCC impact is. Findings from the UIA SCE project have clearly underlined the above mentioned relationship between the way building has been designed and its environmental and economic impact.
UIA SCE Expert’s Journal 4 and 3 elaborated costs and benefits from deconstruction and reuse of 3D units in SCE project. The journals explained in a great length, aspects behind high deconstruction costs and their relation to the complexity of recovery operations which involved coordination of multiple stakeholders (seven different companies were involved in process of hoisting 3D concrete module from 10th story). (Figure 4) Besides great deconstruction management operations, other aspects as (i) safety risks requiring significant preparation and safeguarding of the existing structure, as well as (ii) use of multiple tools and heavy machinery to secure safe hoisting, (iii) transport and placement of the units are behind high deconstruction costs of 3D units form the 10-story building. The reason for this complexity, which is reflected through the costs, is the fact that the structure of the 10-story building was not designed for disassembly and recovery of its parts.
Additional costs related to the deconstruction and reuse of tunnel shaped 3D concrete unit are listed below.
Labour cost for deconstruction |
€ 14.791,38 |
material |
€ 16.671,15 |
equipment |
€ 70.170,38 |
Total deconstruction 3D unit M2 prise deconstruction 3D unit |
€ 101.632,91 € 1.376,- /m2 |
This indicates that only deconstruction costs (€ 1.376,-/m2) already exceeded m2 construction price of linear conventional house (€ 1294,-m2). Construction costs, including deconstruction and reuse of load-bearing structure (tunnel shaped 3D concrete unit) for Type A house amounts €4.273,-/m² excluding VAT. Average m2 price of new conventionally built house is ca € 1294,-m2. That means that SCE house built with recovered concrete 3D unit costs 3,5 times more than conventional house today.
On the other hand, SCE experiments and monitoring concluded that the most economically feasible circular strategy for construction of three new houses was to reuse material on the lower level of building decomposition as element level (building parts) and material level (aggregate for concrete) (Figure 5). Recovery and reuse of building parts on lower levels of building composition will have lower environmental benefits due to the additional CO2 emissions and energy consumption related to their remanufacturing and treatment processes, but will have better financial performance in the context of today’s legislation and market conditions.
The circular concrete technology has been developed further through the SCE project and has been used to build the third house Type C.
Construction costs of this house type excluding VAT is € 163.415,-. M2 price of house type C is +/- €3.026,-/m² excluding VAT which is 2,5 time more than conventional house. However, deconstruction company Dusseldorp (one of the project partners) has improved the fabrication process of recycling concrete after testing its framework through the UIA SCE project. After this optimisation phase, Dusseldorp managed to drastically reduced the cost of this technology. The technology has been applied again in construction of 15 spin-off projects in the circular experimental area in Kerkrade. The project illustrated that after optimisation stages of SCE technology the m2 price of the new 15 circular houses is 20% higher compared to a linear construction which is great improvement compared to 2,5 times higher costs that have been registered during SCE experiments.
Brief summary of conclusions so far
Experiments within the SCE project changed the conventional perception of the end of building life (Figure 4 and 5), illustrating that end of life of a building does not necessarily mean end of product and material life. On the contrary, end of building life can be seen as a “restart” of new life and diversion of building products and materials from landfill and downcycling. Contrary to the conventional demolition process, which has only costs associated to it, circular deconstruction and reuse projects bring benefits into equation that needs to be balanced from project to project.
According to the report J.J.M Zaad 2019 recovery of tunnel shaped concrete 3D module saved 34% of CO2, 34% of embodied energy and 95% of raw materials, compared to conventional construction with concrete which consumes 100% of raw materials, energy and emits 100% of CO2. Regardless of economic impacts, which are not competitive with market conditions and financial models of linear construction today, the SCE project proved that every reuse strategy that has been tested during the project has environmental benefits compared to conventional construction. (Table 1 and 2)
Project 1
Based on the lessons learned from the UIA SCE project and construction of three houses, a strategy has been developed for the construction of new circular 15 houses in the same neighbourhood in Kerkrade (see figure 3). The aim of construction of 15 circular houses was to reuse materials form the neighbouring building block and assemble buildings in a way that will increase disassembly potential and ultimately reuse on product/system level in the future. Project team decided to redesign connections of conventional PlusWonen system and transform it from a static into a dynamic more reversible system by applying dismantlable connections. PlusWonen is conventional building system using prefabricated concrete elements for housing construction. Its conventional connections were not designed for reversibility and reuse of its parts. Redesign of the building connections within a PlusWonen system with disassembly in mind will increase ease of recovery and reuse potential of building parts in other projects in the future.
Having that in mind 15 new houses are built with a modular, prefab and demountable concrete system and products and their connections were designed for disassembly. Some of them are illustrated in the figure 6 bellow (brix wall block, brick demountable façade system) and prefabricated and dismantlable loadbearing system illustrated in figure 10.
Figure 9: Reversible building products used for the construction of 15 new circular houses in Kerkrade
Figure 10: assembly of prefab demountable concrete system and prefab wooden roof components of 15 circular houses in Kerkrade.
Table below illustrates design rules and circular building techniques applied during construction of 15 circular new houses based on lessons learned and technologies developed within the UIA SCE project.
In order to assess costs and benefits of the 15 circular houses, which are constructed with disassembly in mind, Zuyd University of Applied Science compared embodied energy (EE) and embodied CO2 (ECO2) of conventional PlusWonen structure with embodied energy and embodied CO2 consumption of improved PlusWonen structure. Improved PlusWonen structure was made with recycled aggregate while components, elements and connections are improved for higher disassembly potential.
The compressions (based on the calculations done by R. van den Bogert and M. Ritzen) are presented below:
- Environmental impact of PlusWonen system with recycled circular concrete tested in SCE project without reversible solutions and dismantlable connections:
EE (embodied energy) = 1346,8 EE/m2
ECO2 (embodied CO2 emissions) = 152,4 ECO2/m2 (K. Catulini 2021)
- Environmental impact of PlusWonen system with recycled circular concrete and dismantlable connections when PlusWonen system is reused on big scale (e.g 50 apartment)
EE(embodied energy) = 404 EE/m2
ECO2 (embodied CO2 emissions) = 45,7 ECO2/m2 (K. Catulini 2021)
The study indicates that in a big scale reuse projects more reversible PlusWonen building system with high disassembly potential can save up to 70% of Embodied energy and 70% of Embodied CO2 in comparison with conventional PlusWonen system, which is not reversible.
At the same time, it is worth mentioning that economic impacts of such reversible building are more beneficial due to the fact that direct reuse strategies can be applied on most of the components requesting simple deconstruction procedures and equipment.
Project 2
In order to conserve parts of cultural continuity, Municipality of Kerkrade and housing cooperation HeemWonen decided to keep half of the third 10-story block which has iconic value for the community and extend it with additional volume, built with circular techniques developed during the SCE project. (see figure 3 and figure 11)
Besides socio-cultural values, direct reuse of building has also higher positive impacts on the environment and costs. Existing 10-story high apartment block contains 2.3E04 GJ embodied energy 2.9E03 tons of embodied CO2 and 1,38E04 ton of material (M.Ritzen et al. 2019).
By reusing 50% of the block, 690000 tons of material has been directly saved, including 230000 GJ of Embodied energy and 29000 tons of CO2, while material from the other half of the block has been recovered and reused in the construction of the block extension. The reused half of the 10-story block can be seen on figure 14 as well as the start of the construction of the other half of the block with use of recycled material.
Figure 11: half of the 10-story building has been refurbished and other half deconstructed and built with circular building techniques developed during the SCE project.
The figure below illustrates floorplan typologies and façade of the second spin off project with lower part belonging to half of the reused part of the 10-story block and higher part belonging to the re-built half of the block.
The SCE project managed to demonstrate implementation of three alternative circular material streams, originating from the existing 10-story flat building. These alternative circular streams enabled restart of material life through material reuse on different levels of building composition (i) material, (ii) product and (iii) building level. All three reuse levels have been demonstrated within an experimental circular building area in Kerkrade (Figure 3) as a (i) part of the UIA SCE project and (ii) upscaling of SCE techniques through spin off projects.
One can say that experiments within the SCE project changed the conventional perception on the end of building life, illustrating that end of life of a building does not necessarily mean end of product and material life. On the contrary, end of building life can be seen as a “restart” of new life and diversion of building products and materials from landfill and downcycling. Such philosophy is at the core of circular building and circular economy in construction and SCE demonstrated its real life application.
Closing the water cycles
Besides material circularity, the UIA SCE project consortium developed a strategy for closing the water streams within a neighbourhood by collecting water from the buildings and surrounding public spaces and landscape, recycling water in treatment facilities and reusing water streams for different purposes. Figure 12 below illustrates the management system of six water streams managed within the UIA SCE and surrounding area: (i) rainwater, (ii) drinking water, (iii) grey water (shower and kitchen sink) (iv) black water (toilet and biological waste) (v) cleaned grey water and (vi) water for washing machine. Water cycling experiment has been developed in collaboration between the UIA SCE and Life program. (Figure 12)
Figure 12: six water streams managed within the SCE and surrounding area in Kerkrade
Black water stream is organised by separating organic waste and grey waste from the toilets and kitchens. Organic waste from the kitchen and vacuum toilets have been collected in a black water stream and transported for fermentation. Biogas produced by fermentation process is reused for heating needed to support fermentation process. (Figure 13)
Figure 13: collecting water from building, transport to the fermentation installation and reuse of black water stream as compost in the garden.
Second type of water stream comes from shower, kitchen sink and washing machine. So called grey water stream. The grey water is collected from the bathroom and kitchen and recycled with use of algae and helofytenfilter and reused in public fountain for watering the greenery. Recycling and reuse water system is presented in the figure 13.
Figure 13a: Grey water system illustrating collection and treatment of water from shower, kitchen sink and washing machine and reuse for public fountain and watering.
Besides water collection from buildings, its treatment and reuse, rainwater around the buildings as well as from the roofs and streets has also been collected and stored in the dedicated treatment tanks. (Figure 14) Drinkwaterbedrijw WML has tested upcycling of rainwater to drinking water.
Figure 14: rain water collection compartments
Ultimately, each drop of water has been put into a system which is reusing water for different purposes. Integrated concept of treatment and reuse of water in the landscape and public spaces around buildings is presented in figure 15.
Figure 15: treatment and filtering of water through the landscape in the area around SCE circular houses and spin off projects.
Social and cultural continuity boosted by circularity
One of the key objectives of the UIA SCE project was to enable social circularity by involving former inhabitants during design of transformation of urban area, shared facilities, and circular housing. The aim was to create greater participation and ownership of the development within the community by stimulating return of inhabitants after the transformation process.
Number of co-creation sessions with inhabitants have been organised, which resulted into their involvement into a physical transformation of the neighbourhood that brought about greater social interactions. The community was involved in shaping shared facilities, social plinth with washing space, reparation space, gathering space, mobility space. (Figure 19)
Figure 16: few functions of shared facilities as part of the UIA SCE project
Inhabitants became an important stakeholder during the urban transformation process. This resulted in partial return of former inhabitants and thus reuse of social capital that will take care of social continuity and cohesion of the neighbourhood in the future. Local community participated in research on social acceptance of circular buildings. The questionnaire carried out by Zuyd University of Applied Science indicated that acceptance of circular building is high if reused parts and materials are either directly visible (as reused crashed façade parts in figure 17) or not visible at all. Solutions in-between are not appreciated by the user. (Zoom in no. 3) Due to the dynamic interactions and involvement of the local community in the process, the SCE project has been embraced by the inhabitants who became proud of what had been achieved, while number of former inhabitants decided to return to the neighbourhood.
Figure 17: First key handed over to the inhabitants
Lessons learned and future actions
The UIA SCE consortium was able to identify some key barriers for the successful scaling up of circular economy in construction. One barrier that need to be looked at carefully are financial incentives whereby carbon pricing may have a role to play. Concern over climate change has led to policies that put a price on carbon emissions using either a market-based emissions trading system (“cap and trade”) or a carbon tax, both of which can affect the operating cost. A well-known example of carbon pricing is the European Union cap-and-trade system. Although carbon prices have tripled under the EU’s Emissions Trading System (EU ETS), the current levels (€18[US$21]/tCO2) are still far below the prices that leading economists say are required to meet the Paris climate goals (US$40-80 by 2020).
https://carbonmarketwatch.org/2018/08/21/netherlands-fits-its-new-price-floor/
In the Climate Change Action Plan, the World Bank committed to support the achievement of global climate change goals. https://static1.squarespace.com/static/54ff9c5ce4b0a53decccfb4c/t/59b7f2409f8dce5316811916/1505227332748/CarbonPricing_FullReport.pdf.
The High-Level Commission on Carbon Prices, concluded that a range of US$40-80 per ton of CO2e in 2020, rising to US$50-100 per ton of CO2e by 2030, leading to values of $156 by 2050 is consistent with achieving the core objective of the Paris Agreement of keeping temperature rise below 2 degrees, provided a supportive policy environment is in place (High-Level Commission, 2017). This is seen by World Bank experts on carbon pricing as conservative assumption reflecting a very optimistic forecast of early mitigation action and rapid cost decline of low-carbon technologies (World Bank 2017). Cost benefits analyses in the SCE project proved this assumption of the World Bank to be true.
If reuse of carbon within the SCE project would be calculated as financial benefit, according to the potential carbon pricing development projected by the World Bank, the gap between construction costs of conventional house presented by Housing corporation HeemWonen and construction cost of SCE House would still remain significantly high at +/- €1.500,-/ m². This indicates that carbon taxing alone cannot bring balance in costs and benefits of projects dealing with conventional building structures, and that besides substantial taxation policies (addressing CO2, labour costs, raw material), significant improvements and standardisations in deconstruction technique are needed, but even more importantly new design and construction standards for future circular/reversible buildings that will enable disassembly and high value reuse of materials after their initial use need to be adopted.
Standards for circular building
Although during construction of SCE House Type A , (i) 90% of row material has been saved (18,5-ton material were directly reused form neighboring donor building), (ii) 46,21 ton CO2 saved and (iii) 33,5 GJ energy saved, these savings of environmental capital were not reflected in construction cost of circular SCE hoses. Construction cost of circular houses was between 2,5 and 3,5 times higher than construction cost of conventional housing project.
SCE consortium concluded that focus on one use cycle of materials from 10-story flat building, will not solve the challenges that circular buildings and circular economy are facing.
Besides the level of deconstruction and reuse of building materials, the SCE experiment illustrated the importance of additional factor in determining feasibility of reuse strategies. This additional factor, which is often put aside in “circular construction projects”, is method of construction and the way building parts are connected. Complex recovery operation around reuse of tunnel shaped 3D concrete units illustrated that shorter material feedback loops are beneficial (from economic and environmental point of view), only if product is designed for disassembly and high value reuse. This means that product should be designed for minimised effort and time needed to recover product from the building. Capacity of buildings to enable high quality material reuse is not determined only by the quality and type of materials in the building but by the way materials are put together and emerged dependences. (Durmisevic 2006)
With this in mind, SCE consortium partner Dusseldorp developed reversible BRX building block with future reuse in mind which has been used during construction of the 15 spin off projects. (Figure 12)
Policy recommendations
Environmental and economic impact of reusing recovered 3D concrete unit from the 10th floor building turned out to be 4 times more expensive than construction of a new wall. When analysing the environmental impact of this operation, it turned out that this operation saves (i) 33,94% of CO2 emissions in comparison with construction of conventional concrete unit, (ii) it saves 34% of energy in comparison with conventional construction and (iii) ca 75% of material value (residual value) has been saved. Considering relatively low CO2 price at the moment, these environmental savings do not compensate the construction costs which are 4 times higher than conventional construction. This is primarily related to the effort needed to recover and reuse 3D unit, 60-man hours compared to 34-man hours needed for conventional construction of a concrete structure. The effort is also reflected in the machinery needed to recover 3D units. Three mobile cranes of 750 ton, 500 ton and 100 tone where used compared to one mobile crane of 50 tone for conventional construction concrete structure.
In order to mitigate the above described disbalance, a number of recomondations can be proposed:
- Internalise external costs (CO2, embodied energy, waste disposal tax, etc.) as building costs
- Standardise circular building quality and introduce a quota for the application of reused elements and recycled materials in new construction and building products.
- Prescribe reversibility index as a part of a new building standard. Reversibility index reflects the reuse options of materials from one building, their damage level and difficulty during recovery (reflected in CO2 and costs).
- Possible options for new taxation policy: Reduce labour tax, increase tax on raw materials, increase tax on Construction and Demolition Waste and introduce disposal fees for projects with low reversibility index/score
- Look into new business models and new roles of stakeholders, such as product or building as a service and contractors as service providers.
- Improve inventory mechanisms to establish overview building’s reversibility and reuse strategies of materials within a building
- Introduce reversibility passport for new products and buildings
- Encourage creation of digital platforms that will bring supply and demand together
Challenges
Risks associated with the delays within the UIA project have been identified timely together with the consortium members. MUA asked active participation of each consortium member in proposing measures as how to mitigate the risks. Due to the delays in construction, few activities such as (i) activation of shared facilities, (ii) monitoring of water recycling and (iii) implementation of mobility services were not finalised within a time-line of the project.
After systematic analysis of impacts of delays on deliverables, the consortium managed to reorganise final activities in a way that they can be finalised during the dissemination year. The solution was found in partial financing of the monitoring of water recycling system by LIFE program and partial financing of the remaining activities by the partners themselves. Such balanced solutions enable the consortium to meet the objectives and to include their results into the final quality report.
Not relevant for this phase. Important procurement issues have been addressed in earlier project phases.
Not relevant for this phase. Important Integrated cross-departmental working issues have been addressed in earlier project phases.
Not relevant for this phase. Participative approach issues have been addressed in earlier project phases.
Monitoring of key project indicators has been intensified as the construction of houses progressed in the last six months. This enabled ZUYD University of Applied Science to apply real time monitoring and testing of different reuse and construction strategies and collect actual data about construction process, construction time, and equipment used on the construction site. Based on this data, impact analyses have been done for 9 deconstruction techniques.
The consortium has built up well organized promotion and image of the project based on well established channels of communication about progress of the SCE project. At the end of the project, the consortium organised an international scientific conference called Crossing Boundaries (Super Circular Estate - Crossing Boundaries 2021) to share lessons learned from the SCE project with broad international audience. Besides, after the completion of the construction of the three houses, the consortium has organised a stakeholder’s event to share the results with local communities and handover the key to the first inhabitants. SuperLocal-NL (tourmkr.com) Thanks to the well-organized promotion, the SCE project have already found application in new local initiatives and spin off projects. Video: overzicht project SUPERLOCAL – SUPERLOCAL
Upscaling of the technologies developed during the SCE project have been applied in the construction of 15 new apartments using demountable prefabricated concrete system made with recycled concreate. Besides this project, other spin off project is under construction concerning partial refurbishment of half of a 10-story housing block and construction of 114 new circular apartments in the other half of the 10-story housing block. Many other projects outside of the region are in preparation stage, promising full application of recycled concrete technology developed by SCE consortium members Dusseldorp in the future.
The UIA SCE project results can be summarised through number of achievements, which dealt with:
- testing deconstruction and circular construction methods,
- reusing 1,38E04 Ton of material and associated 2.3E04 GJ embodied energy,
- reusing 2.9E03 tons of embodied CO2 from 10-story apartment block though the construction of three SCE houses and spin off projects in the super local experimental area in Kerkrade,
- testing social circularity through user participation,
- indicating opportunities and barriers of circular deconstruction/construction based on real-life experience,
- implementing lessons learned and most feasible technologies into scaling up projects, such as construction of 15 circular houses and 141 circular apartments
- (showcasing construction of circular houses that contain 95% of reused/recycled material,
- testing a system for closed water cycles and demonstrating treatment and reuse of 6 types of water streams.
Besides these direct achievements of the SCE project, it also inspired some new developments such as upgrading of existing prefab system for easy disassembly and future reuse of its elements, deconstruction of parking garage in Amsterdam and reuse of its elements in Kerkrade, further development of reversible building products as BRIX developed by Dusseldorp.
At the end of the project, one can say that the SCE project managed to decode the potential of circular economy in construction when exploring the concept of Buildings as Material Banks and harvesting materials from existing buildings for new construction. Project put more light on circularity of the existing housing stock in the Netherlands built in 70s including its expected material streams and associated deconstruction and reuse strategies.
Deconstruction of buildings can effectively improve the overall performance of CDW and reverse “the end of life” of building materials to “restart of new life” of building materials, by enabling high value recovery. However, numerous challenges hinder the high value recovery of building materials. These challenges have been addressed by the UIA SCE project and lessons learned presented in this and previous Expert Journals.
(EU 2018) EU CDW Protocol and Guidelines, 2018
https://ec.europa.eu/growth/content/eu-construction-and-demolition-waste-protocol-0_en
(J.J.M.Zaad 2019) Financiële haalbaarheid SUPERLOCAL, J.J.M Zaad , ZUYD 2019
(Pieter Scheer 2020) BRX by Pieter Scheer, Dusseldorp 2019
(UIA Experts ZOOMIN, 2019) Durmisevic, 2019 UIA Experts ZOOM IN1
(UIA Experts ZOOM IN 2) Durmisevic 2020 UIA Experts ZOOM IN 2
(M.Ritzen, 2019) M. Ritzen at all, Conference proceedings Circular (de)construction in the Supralocal project, SBE19 Brussels BAMB-CIRCPATH, IOP Publisher, 2019
(Durmisevic, 2019) Design strategies for reversible building guidelines , BAMB2020 https://www.bamb2020.eu
(Durmisevic, 2006) Transformable Building Structure – Design for Disassembly as a key to introduce sustainable engineering to building design and construction, E. Durmisevic, Published by TU Delft 2006
(Bogert & Ritzen 2021) R. van den Bogert and M. Ritzen, Environmental impact evaluation of five circular concrete scenarios, ZUYD, Heerlen 2021
(K. Catulini 2021) K. Catulini, Circulariteit PlusWonen en SUPERLOCAL Hoe circulair is PlusWonen bij SUPERLOCAL? Theses publihed by ZUYD, Heerlen 2021
(World Bank 2016) World Bank Group Climate Change Action Plan 2016-2020 (English). Washington, D.C. : World Bank Group.
https://documents.worldbank.org/en/publication/documents-reports/documentdetail/755721468011421594/world-bank-group-climate-change-action-plan-2016-2020
About this resource
The Urban Innovative Actions (UIA) is a European Union initiative that provided funding to urban areas across Europe to test new and unproven solutions to urban challenges. The initiative had a total ERDF budget of €372 million for 2014-2020.
Similar content
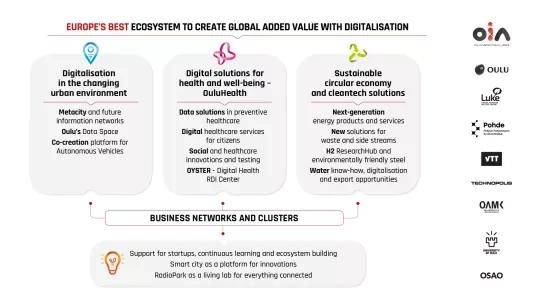
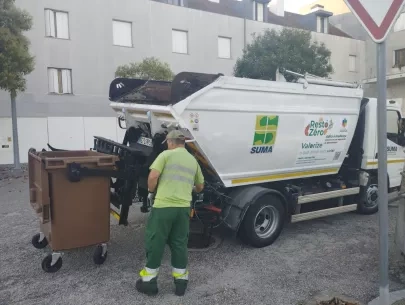
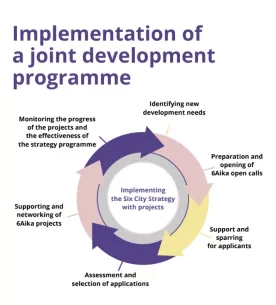